Damping optimization design method, for constraining damping drum, based on modal strain energy method
A modal strain energy and constrained damping technology, applied in computing, mechanical equipment, springs/shock absorbers, etc., can solve the problems of unscientific layout of damping materials and complicated calculation process of damping structure optimization, so as to reduce calculation time and improve The effect of efficiency
- Summary
- Abstract
- Description
- Claims
- Application Information
AI Technical Summary
Problems solved by technology
Method used
Image
Examples
Embodiment Construction
[0033] The present invention will be further described below in conjunction with drawings and embodiments.
[0034] Such as figure 1 The drum shown in the figure uses constrained damping material to suppress the vibration of the drum. The Young's modulus of the drum is 200GPa and the density is 7900Kg / m 3 , Poisson's ratio 0.25; damping layer thickness 0.00005m, Young's modulus 12MPa, density 1200Kg / m 3 , Poisson's ratio 0.495, loss factor 0.5; constrained layer thickness 0.00013m, Young's modulus 70GPa, density 2700Kg / m 3 , Poisson's ratio 0.3. The bolt holes of the drum are fully constrained, and the first-order mode is the focus of attention, and the amount of constrained damping material used is 50% of the full coverage. To optimize the layout of constrained damping materials, the specific steps are:
[0035] 1) Paste the constrained damping material on the inner wall of the aero-engine drum to form the constrained damping drum, establish the finite element model of th...
PUM
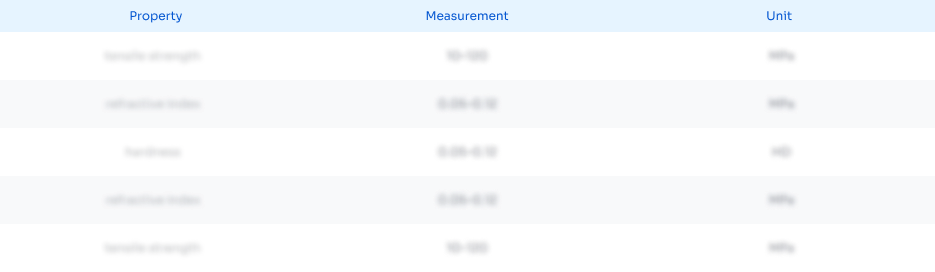
Abstract
Description
Claims
Application Information

- R&D
- Intellectual Property
- Life Sciences
- Materials
- Tech Scout
- Unparalleled Data Quality
- Higher Quality Content
- 60% Fewer Hallucinations
Browse by: Latest US Patents, China's latest patents, Technical Efficacy Thesaurus, Application Domain, Technology Topic, Popular Technical Reports.
© 2025 PatSnap. All rights reserved.Legal|Privacy policy|Modern Slavery Act Transparency Statement|Sitemap|About US| Contact US: help@patsnap.com