Cogging force suppression method for flux-switching linear motor
A linear motor, magnetic flux switching technology, applied in the direction of electronic commutation motor control, motor generator control, AC motor control, etc., can solve the problems of cumbersome and unsuitable harmonic current injection process
- Summary
- Abstract
- Description
- Claims
- Application Information
AI Technical Summary
Problems solved by technology
Method used
Image
Examples
Embodiment Construction
[0034] The present invention will be further described below in conjunction with the accompanying drawings.
[0035] Such as figure 1 , Figure 4 Shown is a positioning force suppression method for flux switching linear motors, which uses a new repetitive controller and position recursive control algorithm to achieve the purpose of suppressing positioning force and speed fluctuations, and at the same time realizes no position sensing technology; specifically includes Follow the steps below:
[0036] (1) Speed given signal Output speed reference value v after passing through the new repetitive controller ref , the new repetitive controller is designed as follows:
[0037] first to Perform Laplace transform to obtain v(s), make difference between v(s) and y(s) to obtain e(s), and perform inverse Laplace transform on e(s) to obtain e(t); then set There must be a linear operator T and an inverse operator T -1 ,calculate and then through k RP Adjust the convergence sp...
PUM
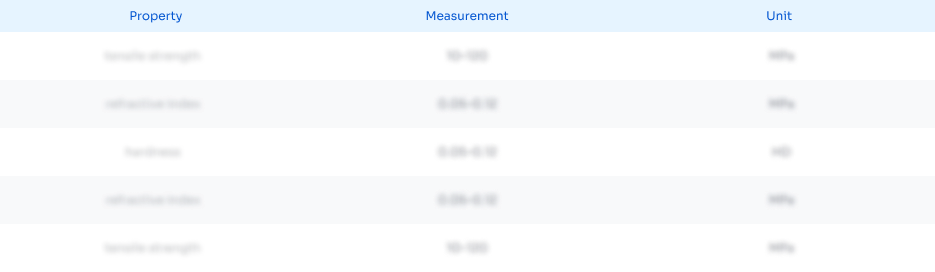
Abstract
Description
Claims
Application Information

- R&D
- Intellectual Property
- Life Sciences
- Materials
- Tech Scout
- Unparalleled Data Quality
- Higher Quality Content
- 60% Fewer Hallucinations
Browse by: Latest US Patents, China's latest patents, Technical Efficacy Thesaurus, Application Domain, Technology Topic, Popular Technical Reports.
© 2025 PatSnap. All rights reserved.Legal|Privacy policy|Modern Slavery Act Transparency Statement|Sitemap|About US| Contact US: help@patsnap.com