Nano caliper based on double-probe AFM and method for measuring key dimension of micro-nano structure through nano caliper
An atomic force microscope, micro-nano structure technology, applied in scanning probe microscopy, measurement devices, optical devices, etc., can solve difficult side wall surface scanning, difficult, difficult adjacent and relative area scanning imaging and measurement issues
- Summary
- Abstract
- Description
- Claims
- Application Information
AI Technical Summary
Problems solved by technology
Method used
Image
Examples
specific Embodiment approach 1
[0046] Specific implementation mode one: combine figure 2 To illustrate this embodiment, the nanocaliper based on a dual-probe atomic force microscope described in this embodiment includes a dual-probe atomic force microscope and two probe racks 24 with the same structure, and the probe rack 24 includes a base 24-1 and a The rotating arm 24-3, the rotating arm 24-3 is arranged on the base 24-1, and the rotating arm 24-3 can rotate around its central axis, and the two bases 24-1 are respectively used for the two probe holders 24 is fixed on the first probe hand 18 and the second probe hand 11 of the double-probe atomic force microscope, and the No. 1 probe and No. 2 probe of the double-probe atomic force microscope are respectively fixed on the rotation of the two probe racks 24. On the arm 24-3, the cross-section of the No. 1 probe is circular or oval, and the No. 2 probe has the same structure as the No. 1 probe.
[0047] The nanocaliper based on the dual-probe atomic force...
specific Embodiment approach 2
[0049] Specific implementation mode two: combination figure 1 and image 3 Describe this embodiment. This embodiment is a further limitation of the nanocaliper based on the dual-probe atomic force microscope described in Embodiment 1. In this embodiment, the dual-probe atomic force microscope includes an optical microscope 1 and a host computer 20 , the first laser mechanics subsystem, the second laser mechanics subsystem, the first probe hand 18, the second probe hand 11, the second XYZ micro-positioning stage 12, the second XYZ nano-positioning stage 13, and the XY micro-positioning stage 14 , the first XYZ nano-positioning stage 15, the sample stage 16 and the first XYZ micro-positioning stage 17, the dual-way probe controller 23, the acquisition card 19, two piezoelectric controllers 21, the No. 1 switcher 22, and the No. 2 switch Device 25 and No. 3 switch 26;
[0050] The first laser mechanics subsystem is used to detect the force signal or resonance signal of the firs...
specific Embodiment approach 3
[0055] Embodiment 3: This embodiment is a further limitation of the nanocaliper based on the dual-probe atomic force microscope described in Embodiment 1. In this embodiment, the dual-way probe controller 23 uses an OC4-Dual probe Dynamic controller implementation.
[0056] The signal bandwidth collected by the OC4-Dual probe dynamic controller can reach 5MHz, which makes the control more stable.
PUM
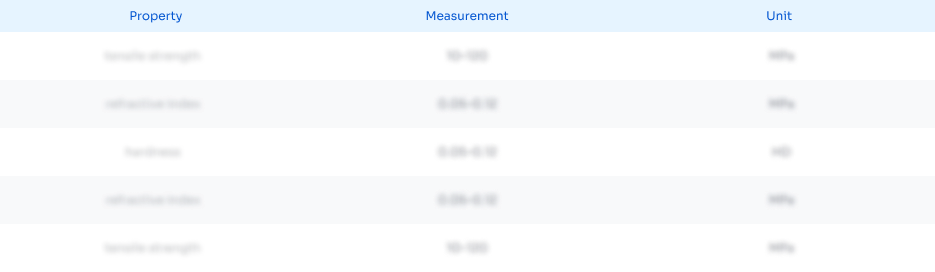
Abstract
Description
Claims
Application Information

- R&D
- Intellectual Property
- Life Sciences
- Materials
- Tech Scout
- Unparalleled Data Quality
- Higher Quality Content
- 60% Fewer Hallucinations
Browse by: Latest US Patents, China's latest patents, Technical Efficacy Thesaurus, Application Domain, Technology Topic, Popular Technical Reports.
© 2025 PatSnap. All rights reserved.Legal|Privacy policy|Modern Slavery Act Transparency Statement|Sitemap|About US| Contact US: help@patsnap.com