Ceramic tile with bulged particle effect and preparation method of ceramic tile
A particle and ceramic tile technology, applied in the field of ceramic tile manufacturing, can solve the problems of poor dry particle bulging effect, uneven cloth, melting glaze, etc., and achieve rich colors and patterns, good uniformity, and large wetting angle. Effect
- Summary
- Abstract
- Description
- Claims
- Application Information
AI Technical Summary
Problems solved by technology
Method used
Image
Examples
preparation example Construction
[0028] Preparation of green body: the present invention can choose conventional ceramic tile green body, and the forming of green body can also adopt common pressing molding. The sintering shrinkage of the green body used can be 8.8-9.2, and the firing temperature of the green body can be 1135-1145°C;
[0029] Apply the top glaze of the above formula on the green body, the thickness of the top glaze can be 0.1-0.2mm, and the sintering temperature of the top glaze is above 1120°C;
[0030] Apply the dry granular glaze slurry of the above formula on the glazed body through a linear glazer, the specific gravity of the dry granular glaze slurry is 1.27-1.38, and the flow rate is controlled between 30-40 seconds;
[0031] Firing: Fire the green body coated with dry granular glaze according to the following firing procedure to obtain ceramic tiles with raised particle effect.
[0032] The firing procedure can be as follows: the highest firing temperature is 1135-1145° C., and the f...
Embodiment 1
[0040] 1) Apply top glaze on the green body. The thickness of the top glaze can be 0.1-0.2mm. The main composition of the top glaze is as described in Table 1:
[0041] Table 1
[0042] SiO 2
al 2 o 3
CaO
MgO
K 2 o
Na 2 o
60.12%
24.22%
0.15%
0.23%
3.97%
2.63%
[0043] The sintering temperature of the surface glaze is 1120°C;
[0044] 2) Preparation of dry granules: the high-temperature frit (50-55% SiO 2 , 20-24%Al 2 o 3 , 0.2~0.5% Fe 2 o 3 , 0.5-1.2% CaO, 0.4-0.7% MgO, 2.0-2.8% K 2 O, 2.9~3.8%Na 2 O) broken and sieved, crushed to 150-200 mesh;
[0045] 3) Preparation of dry granule glaze slurry: configure dry granule glaze slurry with the following weight ratio:
[0046] Dry granules of the above: 30 servings
[0047] Ink ink with a flow rate of 24-30 seconds: 100 parts
[0048] Fixative: 3 parts;
[0049] The specific gravity of the configured dry glaze slurry is 1.32;
[0050] 4) Drizzle d...
PUM
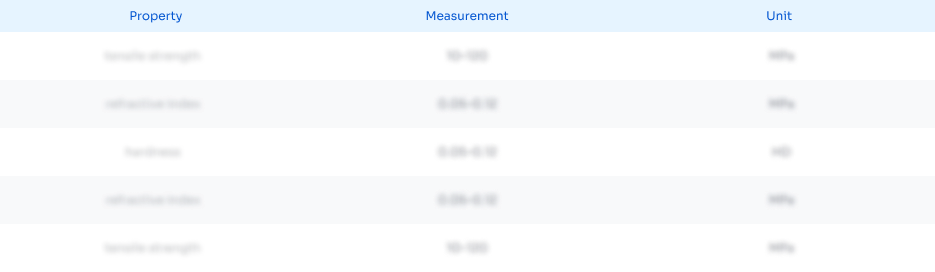
Abstract
Description
Claims
Application Information

- R&D
- Intellectual Property
- Life Sciences
- Materials
- Tech Scout
- Unparalleled Data Quality
- Higher Quality Content
- 60% Fewer Hallucinations
Browse by: Latest US Patents, China's latest patents, Technical Efficacy Thesaurus, Application Domain, Technology Topic, Popular Technical Reports.
© 2025 PatSnap. All rights reserved.Legal|Privacy policy|Modern Slavery Act Transparency Statement|Sitemap|About US| Contact US: help@patsnap.com