Five-axis multi-row flank milling cutter position planning method
A tool position and side milling technology, applied in the direction of electrical program control, digital control, etc., can solve the problems of large space distortion, inability to use one side milling pass, and difficulty in improving processing efficiency and surface quality at the same time
- Summary
- Abstract
- Description
- Claims
- Application Information
AI Technical Summary
Problems solved by technology
Method used
Image
Examples
Embodiment Construction
[0055] The present invention will be described in detail below in conjunction with specific embodiments. The following examples will help those skilled in the art to further understand the present invention, but do not limit the present invention in any form. It should be noted that those skilled in the art can make several modifications and improvements without departing from the concept of the present invention. These all belong to the protection scope of the present invention.
[0056] In this example, if figure 1 , figure 2 , image 3 , Figure 4 as well as Figure 5 As shown, the present invention establishes the tangential continuous condition of the envelope surfaces of two adjacent rows of cutters by utilizing the double-parameter spherical family envelope theory.
[0057] According to the double-parameter spherical family envelope theory, the envelope surface of two adjacent rows of cutters is expressed as
[0058] x (i) (a,t)=S (i) (a,t)+r(a)n (i) (a,t),(a...
PUM
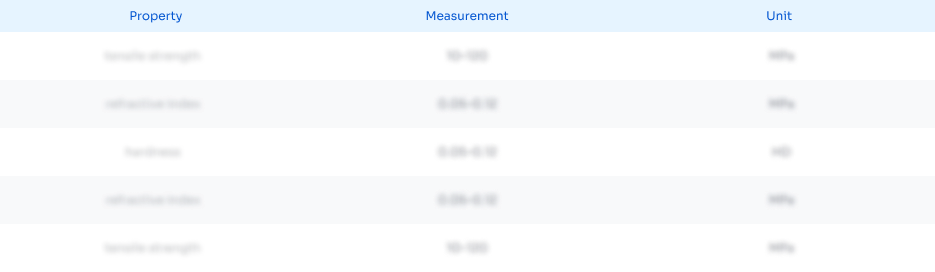
Abstract
Description
Claims
Application Information

- Generate Ideas
- Intellectual Property
- Life Sciences
- Materials
- Tech Scout
- Unparalleled Data Quality
- Higher Quality Content
- 60% Fewer Hallucinations
Browse by: Latest US Patents, China's latest patents, Technical Efficacy Thesaurus, Application Domain, Technology Topic, Popular Technical Reports.
© 2025 PatSnap. All rights reserved.Legal|Privacy policy|Modern Slavery Act Transparency Statement|Sitemap|About US| Contact US: help@patsnap.com