Automatic output device of rotary cutter veneer production line
An automatic output and production line technology, applied in transportation and packaging, sending objects, thin material handling, etc., can solve the problems affecting the stacking quality of standard veneers, wasting raw materials, and breaking veneers, achieving novel structure and high production efficiency. , The effect of low labor cost
- Summary
- Abstract
- Description
- Claims
- Application Information
AI Technical Summary
Problems solved by technology
Method used
Image
Examples
Embodiment Construction
[0023] Below in conjunction with accompanying drawing, the present invention is further described:
[0024] as attached figure 1 , 2 , 3, 4, 5, and 9, an automatic output device for a veneer production line of a rotary cutting machine, which is provided with a conveying frame 1, is characterized in that the rear end of the conveying frame 1 is provided with an automatic grading and stacking device, and the automatic grading and stacking The stacking device is composed of grading frame, swing cylinder 3, swing frame 4, support frame 5, cylinder positioning frame 6, rotating shaft 7, driving pulley 8, pulley bracket 9, pulley 10, grading conveyor belt 11, cylinder seat 13, Photoelectric switch and conveying motor 14 are made up of, and described grading frame is fixedly supported by top frame 2 and four pillars 12 of top frame 2 lower ends, and the top frame 2 of described grading frame is provided with cylinder positioning frame 6, and described grading frame A conveying mot...
PUM
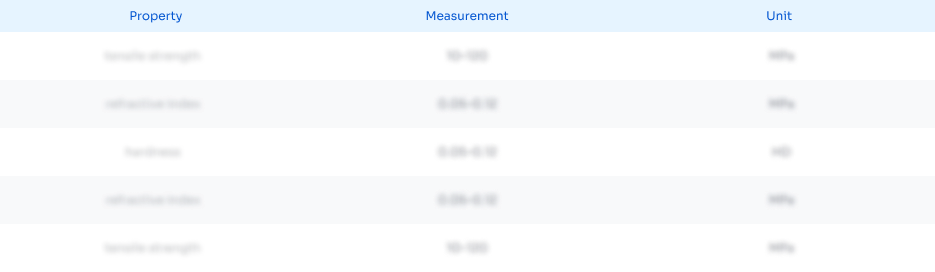
Abstract
Description
Claims
Application Information

- Generate Ideas
- Intellectual Property
- Life Sciences
- Materials
- Tech Scout
- Unparalleled Data Quality
- Higher Quality Content
- 60% Fewer Hallucinations
Browse by: Latest US Patents, China's latest patents, Technical Efficacy Thesaurus, Application Domain, Technology Topic, Popular Technical Reports.
© 2025 PatSnap. All rights reserved.Legal|Privacy policy|Modern Slavery Act Transparency Statement|Sitemap|About US| Contact US: help@patsnap.com