Method for manufacturing capacitance type micro-silicon microphone
A silicon microphone and manufacturing method technology, applied in electrical components, sensors, etc., can solve the problems of small effect, buckling of the vibrating body, complicated processing technology, etc., and achieve the effect of reducing the impact, reducing the volume, and improving the sensitivity
- Summary
- Abstract
- Description
- Claims
- Application Information
AI Technical Summary
Problems solved by technology
Method used
Image
Examples
Embodiment Construction
[0033] See figure 1 and Figure 12 The capacitive microsilicon microphone in one embodiment of the present invention includes a substrate 1 with a front surface 11 and a back surface 12, a movable sensitive layer 3 arranged on the front surface 11 of the substrate 1 and having a conductive function, and arranged on the movable sensitive layer 3 And the back electrode plate 72 with conductive function, the first supporting part 23 arranged between the front surface 11 of the substrate 1 and the movable sensitive layer 3 and used to support the movable sensitive layer 3, the first supporting part 23 arranged between the movable sensitive layer 3 and the back Between the pole plates 72 and used to support the second support portion 62 of the back pole plate 72, several metal pads 14 respectively formed on the movable sensitive layer 3 and the back pole plate 72, and formed on the back pole plate 72 and the back pole plate 72 The cavity 8 between the movable sensitive layers 3 . ...
PUM
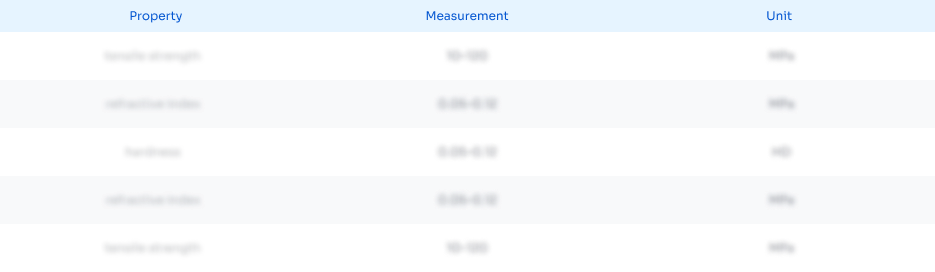
Abstract
Description
Claims
Application Information

- Generate Ideas
- Intellectual Property
- Life Sciences
- Materials
- Tech Scout
- Unparalleled Data Quality
- Higher Quality Content
- 60% Fewer Hallucinations
Browse by: Latest US Patents, China's latest patents, Technical Efficacy Thesaurus, Application Domain, Technology Topic, Popular Technical Reports.
© 2025 PatSnap. All rights reserved.Legal|Privacy policy|Modern Slavery Act Transparency Statement|Sitemap|About US| Contact US: help@patsnap.com