Catalyst loading method for isothermal reactor
A technology for isothermal reactors and catalysts, applied in chemical instruments and methods, organic chemistry, chemical recovery, etc., can solve the problems of low butadiene selectivity, catalyst carbon deposition regeneration cycle, etc., to improve conversion rate and selectivity, The effect of saving product yield and improving production capacity
- Summary
- Abstract
- Description
- Claims
- Application Information
AI Technical Summary
Problems solved by technology
Method used
Image
Examples
Embodiment 1
[0030] A 200,000 tons / year butene oxidative dehydrogenation to butadiene plant adopts figure 1 The reactor is an isothermal tubular fixed bed reactor, the size of the reactor is Φ4500×6000mm, the tubes are Φ50×6000mm, the number of tubes is 4000, and the heat exchange area is 3900m 2 , the catalyst is two kinds of A agent and B agent, A agent is an iron-based composite oxide catalyst, and its general formula is Fe according to its chemical composition. 2 o 3 · MgO · ZnO · P 2 o 5 · CuO, Fe 2 o 3 66% of the catalyst weight, MgO is 20% of the catalyst weight, ZnO is 10% of the catalyst weight, P 2 o 5 CuO is 2% of the weight of the catalyst, and CuO is 2% of the weight of the catalyst, prepared by coprecipitation; agent B is an iron oxide catalyst, the weight content of iron, zinc, and magnesium oxide is 40%, and the weight content of inert alumina is 60% %, the molar ratio of iron, zinc and magnesium is: Fe:Zn:Mg=10:3:5, and the main crystal phase is ZnFe 2 o 4 Spinel,...
Embodiment 2
[0035] A 200,000 tons / year butene oxidative dehydrogenation to butadiene plant adopts figure 1 The reactor is an isothermal tubular fixed bed reactor, the size of the reactor is Φ4500×6000mm, the tubes are Φ50×6000mm, the number of tubes is 4000, and the heat exchange area is 3900m 2 , the catalyst is two kinds of A agent and B agent, A agent is an iron-based composite oxide catalyst, and its general formula is Fe according to its chemical composition. 2 o 3 · MgO · ZnO · P 2 o 5 · MnO 2 , Fe 2 o 3 66% of the catalyst weight, MgO is 20% of the catalyst weight, ZnO is 10% of the catalyst weight, P 2 o 5 2% of catalyst weight, MnO 2 It is 2% of the weight of the catalyst, prepared by co-precipitation method; agent B is an iron-based oxide catalyst, the weight content of iron, zinc, and magnesium oxide is 40%, the weight content of inert alumina is 60%, and the molar content of iron, zinc, and magnesium The ratio is: Fe:Zn:Mg=10:3:5, the main crystal phase is ZnFe 2 o ...
Embodiment 3
[0040] A 200,000 tons / year butene oxidative dehydrogenation to butadiene plant adopts figure 1 The reactor is an isothermal tubular fixed-bed reactor, the size of the reactor is Φ4000×6000mm, the tubes are Φ50×6000mm, the number of tubes is 3400, and the heat exchange area is 3300m 2 , the catalyst is two kinds of A agent and B agent, A agent is an iron-based composite oxide catalyst, and its general formula is Fe according to its chemical composition. 2 o 3 · MgO · ZnO · P 2 o 5 · NiO, Fe 2 o 3 62% of the catalyst weight, MgO is 21% of the catalyst weight, ZnO is 12% of the catalyst weight, P 2 o 5 It is 2% of the weight of the catalyst, and NiO is 3% of the weight of the catalyst. It is prepared by co-precipitation method; agent B is inert alumina ceramic balls, and the tubes are divided into 4 filling areas from the inlet of the reaction gas to the outlet, and the filling areas are segmented The length and the content of A and B agents are shown in Table 3. The tota...
PUM
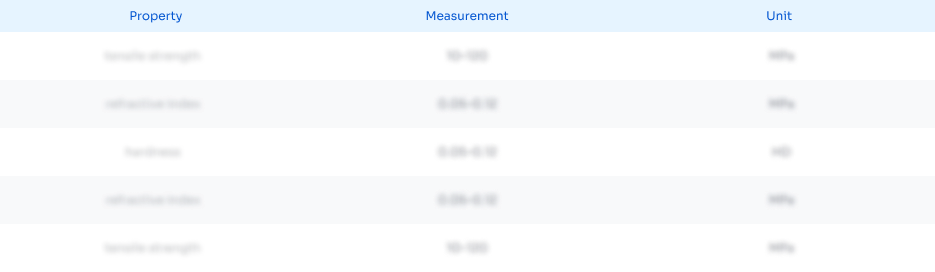
Abstract
Description
Claims
Application Information

- R&D Engineer
- R&D Manager
- IP Professional
- Industry Leading Data Capabilities
- Powerful AI technology
- Patent DNA Extraction
Browse by: Latest US Patents, China's latest patents, Technical Efficacy Thesaurus, Application Domain, Technology Topic, Popular Technical Reports.
© 2024 PatSnap. All rights reserved.Legal|Privacy policy|Modern Slavery Act Transparency Statement|Sitemap|About US| Contact US: help@patsnap.com