Spring pressure friction gear mesh clutch
A spring pressure, clutch technology, applied in the field of clutch and gear transmission, can solve the problems of large volume, low power transmission efficiency, wide structure, etc., and achieve the effect of high transmission efficiency, optimized structure, and small volume
- Summary
- Abstract
- Description
- Claims
- Application Information
AI Technical Summary
Problems solved by technology
Method used
Image
Examples
Embodiment Construction
[0017] exist figure 1 In the embodiment shown in -4: the spring pressure friction gear engagement clutch comprises a driving shaft and a group of driving wheels and a group of driven wheels sleeved on the driving shaft; it is characterized in that: the right section of the driving shaft 1 has a driving Shaft saber teeth 14, a group of driving wheels are set on the driving shaft flower saber teeth 14, the driving wheel 12 has inner flower saber teeth 17 of the driving wheel, and the inner flower saber teeth 17 of the driving wheel are meshed with the driving shaft flower saber teeth 14, the driving The wheel 12 can move along the axial direction of the driving shaft 1, and the driving wheel 12 and the driving shaft 1 rotate at the same angular velocity; the outer circumference of the driving wheel 12 is equipped with a driving wheel outer wheel 9, and the outer circumference of the driving wheel 12 has a plurality of outer foil grooves 16 of the driving wheel , fit with a plura...
PUM
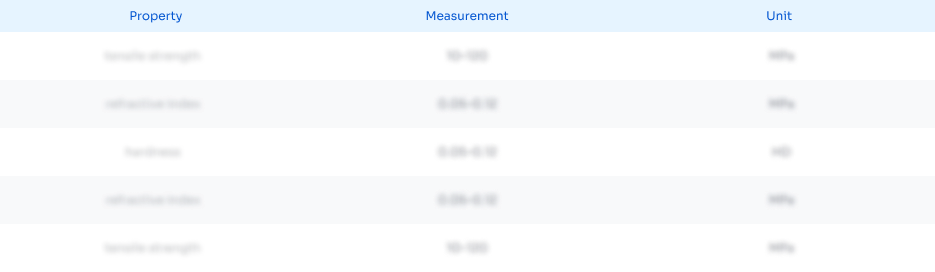
Abstract
Description
Claims
Application Information

- R&D
- Intellectual Property
- Life Sciences
- Materials
- Tech Scout
- Unparalleled Data Quality
- Higher Quality Content
- 60% Fewer Hallucinations
Browse by: Latest US Patents, China's latest patents, Technical Efficacy Thesaurus, Application Domain, Technology Topic, Popular Technical Reports.
© 2025 PatSnap. All rights reserved.Legal|Privacy policy|Modern Slavery Act Transparency Statement|Sitemap|About US| Contact US: help@patsnap.com