Integral hollow composite material firing box cover
A composite material, the overall hollow technology, applied in the direction of the launcher and other directions, can solve the problems of difficult quality stability control, many layers of woven fabrics, and a large separation area, so as to improve the combat response capability, the production process is simple, and the Actionable effect
- Summary
- Abstract
- Description
- Claims
- Application Information
AI Technical Summary
Problems solved by technology
Method used
Image
Examples
Embodiment 1
[0025] Such as figure 1 As shown, an integral hollow composite material launch box cover is mainly designed and manufactured with glass fiber cloth, integral hollow fabric and epoxy resin glue as the main materials. Specifically, the integral hollow composite launch case cover of the present invention mainly includes: 1. a frame, the frame is square, with rounded transitions around; 2. a separation area, the separation area is located between the frame and the throwing The joint of the body is the glued part of the double V-shaped chamfering area; 3. The throwing body, the throwing body forms a square with rounded transitions with the frame, and the overall hollow fabric is used as the sandwich layer.
[0026] The cross-sectional structure of the integral hollow composite launch box cover is as follows: figure 2 As shown, the overall hollow fabric (4) is located in the center of the throwing body, and the upper and lower sides are laminated with a composite material layer (t...
Embodiment 2
[0028] Such as Figure 4 As shown, an integral hollow composite launch box cover is mainly designed and manufactured with glass fiber cloth, integral hollow fabric and epoxy resin as the main materials. Specifically, the integral hollow composite launch case cover of the present invention mainly includes: 1. frame, the frame is circular; V-shaped chamfering area bonding part; 3. Throwing body, the throwing body is formed into a circle with the frame, and the whole hollow fabric is used as the sandwich layer. Its layering method, sandwich structure and separation zone structure form are the same as those in Example 1. This embodiment is equipped with the launch box cover of this shape according to the circular missile launch box. This structure has uniform force, and does not need to consider the prominent stress concentration phenomenon that occurs at the corner. Therefore, the integral hollow composite launch box cover has better performance stability.
Embodiment 3
[0030] Such as Figure 5 As shown, an integral hollow composite launch box cover is mainly designed and manufactured with glass fiber cloth, integral hollow fabric and epoxy resin as the main materials. Specifically, the integral hollow composite launch box cover of the present invention mainly includes: 1. a frame, the frame is hexagonal, with rounded transitions around; 2. a separation area, the separation area is located between the frame and the throw The connecting part of the exit body is the glued part of the double V-shaped chamfering area; 3. The throwing body, the throwing body forms a hexagonal shape with rounded corners along with the frame, and the overall hollow fabric is used as the sandwich layer. Its layering method, sandwich structure and separation zone structure form are the same as those in Example 1. This embodiment is used in a hexagonal launching box structure, and also has better sealing performance, stability and pressure bearing capacity.
PUM
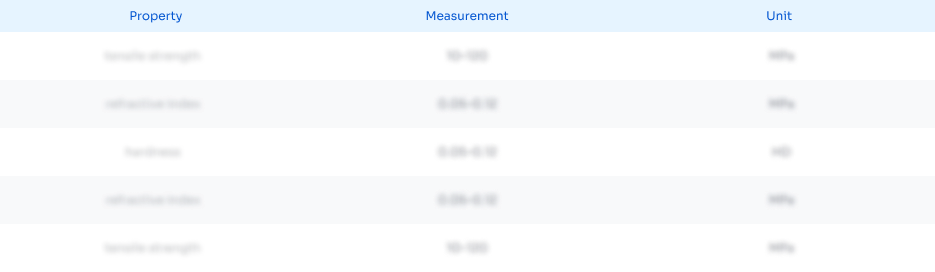
Abstract
Description
Claims
Application Information

- R&D
- Intellectual Property
- Life Sciences
- Materials
- Tech Scout
- Unparalleled Data Quality
- Higher Quality Content
- 60% Fewer Hallucinations
Browse by: Latest US Patents, China's latest patents, Technical Efficacy Thesaurus, Application Domain, Technology Topic, Popular Technical Reports.
© 2025 PatSnap. All rights reserved.Legal|Privacy policy|Modern Slavery Act Transparency Statement|Sitemap|About US| Contact US: help@patsnap.com