Single-degree-of-freedom joint mechanical driven by two pneumatic artificial muscle assemblies
A pneumatic artificial muscle and degree of freedom technology, applied in the field of bionic robots, can solve the problems of not being able to simulate the flexibility of biological muscles well, the overall weight of the robot is high, and the bionic effect is poor, so as to achieve outstanding bionic features, reduce the weight of joint structures, and improve The effect of flexibility
- Summary
- Abstract
- Description
- Claims
- Application Information
AI Technical Summary
Problems solved by technology
Method used
Image
Examples
Embodiment 1
[0016] Such as Figure 1~Figure 2 As shown, the single-degree-of-freedom joint mechanism driven by dual pneumatic artificial muscles includes two pneumatic artificial muscle components (Ⅰ), two rotating parts (II), a thigh skeleton (Ⅲ) and a calf skeleton (Ⅳ). The two pneumatic artificial muscle components (I) are arranged in parallel on both sides of the thigh frame (III), and the upper ends of the two pneumatic artificial muscle components (I) are connected to the two rotating parts (II) respectively, and The lower ends are rotatably connected with the lower leg frame (Ⅳ); the thigh frame (Ⅲ) includes an "I"-shaped piece (12), a rectangular strip (13) and a fork (14), and the rectangular strip (13 ) are respectively fixed and connected with the "I"-shaped piece (12) and the fork-shaped piece (14) by screws; The skeleton (15) and the lower leg skeleton (16) are fixedly connected by screws; the fork (14) of the thigh skeleton (Ⅲ) is connected to the lower leg of the lower leg...
Embodiment 2
[0018] This embodiment is basically the same as Embodiment 1, and the special features are as follows:
[0019] The pneumatic artificial muscle assembly (I) includes a pneumatic artificial muscle (1), a moving pair connector (4), a trachea joint (6), a round nut (7), a rotating pair connector (8) and a large washer (5 ), the two ends of the pneumatic artificial muscle (1) are fixedly connected with the moving pair connector (4) and the trachea joint (6) through threads; the rotating pair connector (8) and the trachea connector (6) are threaded Fixed connection; the rotating pair connecting piece (8) forms a rotating pair with the lower leg upper frame (15) through the pin shaft (9); the large washer (5) is fixed on the moving pair connecting piece (4) by using a nut and a spring washer ; The axial assembly length of the pneumatic artificial muscle assembly (I) can be fine-tuned through the round nut (7).
[0020] The rotating part (II) includes a bearing connecting part (2) a...
PUM
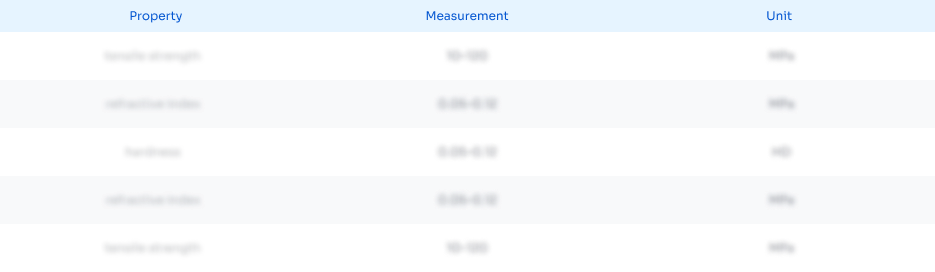
Abstract
Description
Claims
Application Information

- R&D Engineer
- R&D Manager
- IP Professional
- Industry Leading Data Capabilities
- Powerful AI technology
- Patent DNA Extraction
Browse by: Latest US Patents, China's latest patents, Technical Efficacy Thesaurus, Application Domain, Technology Topic, Popular Technical Reports.
© 2024 PatSnap. All rights reserved.Legal|Privacy policy|Modern Slavery Act Transparency Statement|Sitemap|About US| Contact US: help@patsnap.com