Material layer structure of blast furnace
A material layer structure and blast furnace technology, applied in blast furnaces, blast furnace details, furnaces, etc., can solve the problems of reducing production costs, iron-free iron content, coke consumption, etc., and achieve the effect of avoiding waste of energy
- Summary
- Abstract
- Description
- Claims
- Application Information
AI Technical Summary
Problems solved by technology
Method used
Image
Examples
specific Embodiment approach
[0019] Specific implementation: such as figure 1 As shown, a blast furnace material layer structure includes mineral material and coke filled on the upper part of the blast furnace shaft 1, and the mineral material and coke are separately filled to form a mixed mineral layer 3 and a coke layer 2. The coke layer 2 and the mixed ore layer 3 are arranged at intervals and cyclically reciprocate. A single pellet ore layer 4 is also provided between the coke layer 2 and the mixed ore layer 3. The single pellet ore layer 4 can be added to the new material layer structure as a component of the entire material layer structure, and the single pellet ore layer 4 can be used as a replacement for the mixed ore layer 3.
[0020] In addition, because the high-temperature zone of the blast furnace is in the lower part, the high-temperature melting reaction occurs in the lower part of the blast furnace body. Therefore, the ore on the upper part of the blast furnace body is still "lumpy". It can b...
PUM
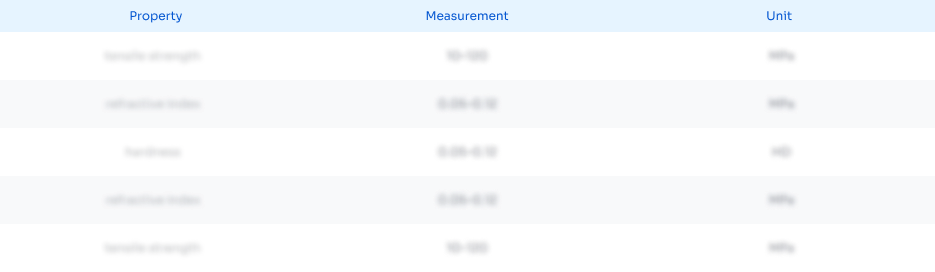
Abstract
Description
Claims
Application Information

- R&D
- Intellectual Property
- Life Sciences
- Materials
- Tech Scout
- Unparalleled Data Quality
- Higher Quality Content
- 60% Fewer Hallucinations
Browse by: Latest US Patents, China's latest patents, Technical Efficacy Thesaurus, Application Domain, Technology Topic, Popular Technical Reports.
© 2025 PatSnap. All rights reserved.Legal|Privacy policy|Modern Slavery Act Transparency Statement|Sitemap|About US| Contact US: help@patsnap.com