A Modular Reconfigurable Flexible Cable Parallel Mechanism Experiment Platform
An experimental platform and modular technology, applied in manipulators, program-controlled manipulators, manufacturing tools, etc., can solve problems such as restricting high load and large workspace tasks, and achieve convenient and flexible assembly and disassembly, simple module structure, and convenient operation. Effect
- Summary
- Abstract
- Description
- Claims
- Application Information
AI Technical Summary
Problems solved by technology
Method used
Image
Examples
Embodiment 1
[0023] figure 1 Shown is an experimental platform for a six-degree-of-freedom flexible cable parallel mechanism. The flexible cable pillars are set in six groups, and the connection points corresponding to the end effector 1 are evenly distributed and located on the outer circumference of the upper table of the end effector 1 and On the outer peripheral surface of the lower table, the connecting points on the outer peripheral surface of the upper table and the outer peripheral surface of the lower table are equidistantly staggered at circumferential positions.
[0024] In specific implementation, for figure 1 In the six-degree-of-freedom flexible cable parallel mechanism experimental platform shown, there are three connection points evenly distributed on the outer peripheral surface of the upper table of the end effector 1, and the other three connection points that are staggered one by one in the circumferential position are evenly distributed On the outer peripheral surface...
Embodiment 2
[0028] The difference from Example 1 is that for the flexible cable parallel mechanism experiment platform with five degrees of freedom, the flexible cable pillars are set in five groups, among which there are three connection points evenly distributed on the outer peripheral surface of the upper table, which are different from those in the circumferential position The other two connection points that form a one-to-one staggered pattern are evenly distributed on the outer peripheral surface of the lower table, and the orthographic projections of a total of five connection points on the plane of the lower table of the conical frustum are located at the five vertices of the regular pentagon.
Embodiment 3
[0030] The difference from Example 1 is that for the flexible cable parallel mechanism experimental platform with four degrees of freedom, the flexible cable pillars are set in four groups, in which there are two connection points evenly distributed on the outer circumference of the upper table, and the The other two connection points that form a one-to-one staggered position are evenly distributed on the outer peripheral surface of the lower platform, and the orthographic projections of a total of four connection points on the lower platform plane of the conical frustum are located at the four vertices of the regular quadrilateral.
PUM
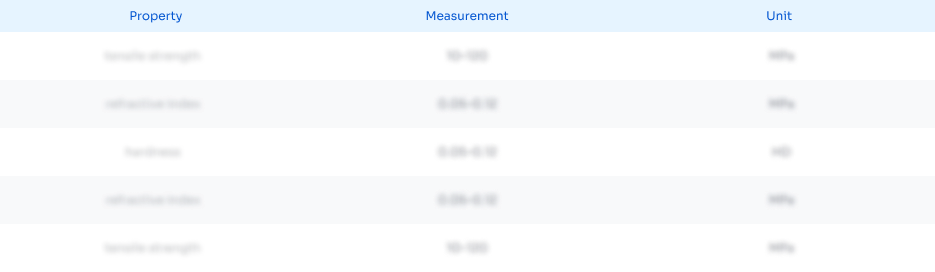
Abstract
Description
Claims
Application Information

- R&D
- Intellectual Property
- Life Sciences
- Materials
- Tech Scout
- Unparalleled Data Quality
- Higher Quality Content
- 60% Fewer Hallucinations
Browse by: Latest US Patents, China's latest patents, Technical Efficacy Thesaurus, Application Domain, Technology Topic, Popular Technical Reports.
© 2025 PatSnap. All rights reserved.Legal|Privacy policy|Modern Slavery Act Transparency Statement|Sitemap|About US| Contact US: help@patsnap.com