Mechanical arm
A technology of mechanical arms and tensioning mechanisms, applied in the direction of mechanical arms, claw arms, manufacturing tools, etc., can solve the problems of inflexible operation of mechanical arms, small routing space of mechanical arms, and low rigidity of mechanical arms, and achieve radial space utilization The effect of high efficiency, space optimization of the robot arm, and strengthening of the arm structure
- Summary
- Abstract
- Description
- Claims
- Application Information
AI Technical Summary
Problems solved by technology
Method used
Image
Examples
Embodiment Construction
[0028] In the following detailed description of the invention, numerous specific details are set forth in order to provide a thorough understanding of the invention. It will be apparent, however, to one skilled in the art that the present invention may be practiced without these specific details. In addition, the present invention will be described below with reference to specific embodiments and drawings.
[0029] Such as figure 1 As shown, the mechanical arm of the embodiment of the present invention includes a housing 1, a sleeve 2, a bearing 3, a pulley shaft 4, a transmission axis 5, a shaft 6, a pulley 7, a transmission belt 8, a tensioning mechanism 9, a pulley 10, and a bearing 11 , Gland 12, housing 13, bearing 14, shaft 15, transmission axis 16, pulley shaft 17, sleeve 18, pulley 19 and screw power transmission cable 20. Wherein, the housing 13 is rotationally connected to the pulley shaft 17 through the bearing 14, the bearing 14 is supported on the pulley 19 thro...
PUM
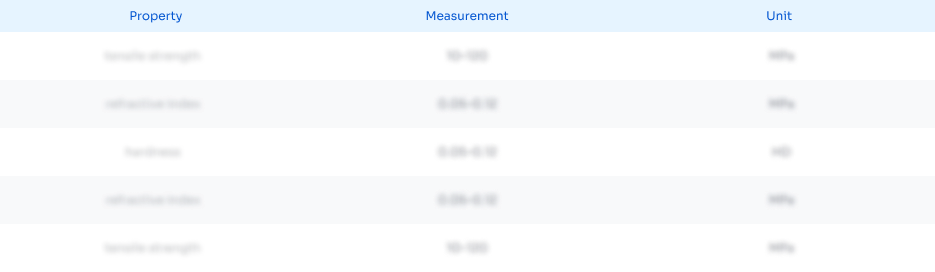
Abstract
Description
Claims
Application Information

- Generate Ideas
- Intellectual Property
- Life Sciences
- Materials
- Tech Scout
- Unparalleled Data Quality
- Higher Quality Content
- 60% Fewer Hallucinations
Browse by: Latest US Patents, China's latest patents, Technical Efficacy Thesaurus, Application Domain, Technology Topic, Popular Technical Reports.
© 2025 PatSnap. All rights reserved.Legal|Privacy policy|Modern Slavery Act Transparency Statement|Sitemap|About US| Contact US: help@patsnap.com