Welding rotatable work fixture for automobile front bumper beam sub assembly
A tooling fixture and front buffer technology, which is applied in the field of rotatable tooling fixtures for welding of automobile front buffer beam sub-assemblies, can solve problems such as affecting production efficiency, high labor intensity, and increasing labor intensity of operators, so as to improve welding processing efficiency, The effect of reducing labor intensity and excellent product quality
- Summary
- Abstract
- Description
- Claims
- Application Information
AI Technical Summary
Problems solved by technology
Method used
Image
Examples
Embodiment Construction
[0015] Depend on figure 1 , figure 2 It is known that a welding rotatable fixture of the front buffer beam subassembly of an automobile is composed of a base 1, a flipping motor 2, a foot switch 3, a flipping floor assembly 4, a six-way adjustment main positioning mechanism 5, and a left side compression cylinder mechanism 6. Six-direction adjustment auxiliary positioning mechanism machine 7. Right side compression cylinder mechanism 8. Front compression cylinder mechanism 9. Assembly six-direction adjustment positioning mechanism 10. Compression hand pliers 11. Supporting cylinder mechanism 12. Compression cylinder The control valve 13, the supporting cylinder control valve 14, and the reduction box 15 are composed; the turning motor 2 and the reducing box 15 are installed on the right side of the base 1, and the turning bottom plate assembly 4 is installed on the left side, and the turning bottom plate assembly 4 and the turning motor 2 pass through Bolts are fixedly conne...
PUM
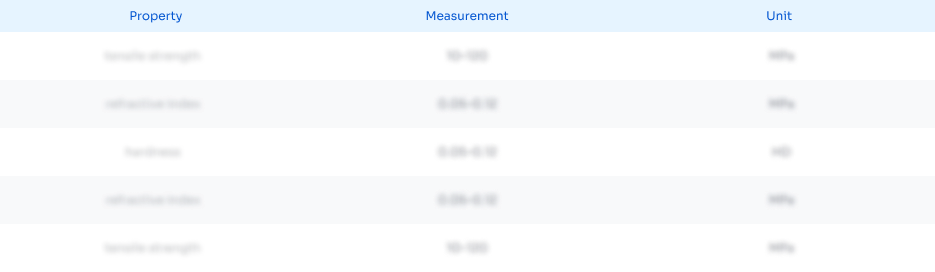
Abstract
Description
Claims
Application Information

- R&D Engineer
- R&D Manager
- IP Professional
- Industry Leading Data Capabilities
- Powerful AI technology
- Patent DNA Extraction
Browse by: Latest US Patents, China's latest patents, Technical Efficacy Thesaurus, Application Domain, Technology Topic, Popular Technical Reports.
© 2024 PatSnap. All rights reserved.Legal|Privacy policy|Modern Slavery Act Transparency Statement|Sitemap|About US| Contact US: help@patsnap.com