Method for preparing magnesium oxide composite fiber
A technology of composite fiber and magnesium oxide, which is applied in the fields of fiber chemical characteristics, textiles and papermaking, can solve the problems of large fiber diameter, unevenness, poor continuity, etc., and achieve smooth surface, reduced fiber diameter, and long aspect ratio Effect
- Summary
- Abstract
- Description
- Claims
- Application Information
AI Technical Summary
Problems solved by technology
Method used
Image
Examples
Embodiment 1
[0022] a. Preparation of spinnable gel
[0023] Dissolve 1.0 g of polyvinylpyrrolidone in 50 mL of deionized water, stir to dissolve, add 2.0 g of magnesium chloride, and stir for 8 hours to obtain a transparent and stable solution. The solution is concentrated by rotary evaporation to obtain a transparent spinnable gel.
[0024] b. Fiber preparation
[0025] After the above gel was left for 3 days, the filaments were picked with a glass rod to obtain composite gel filaments, dried in an oven at 100°C for 24 hours, and then calcined at 450°C to obtain magnesium oxide composite fibers.
Embodiment 2
[0027] a. Preparation of spinnable gel
[0028] Dissolve 1.0 g of polyvinylpyrrolidone in 80 mL of ethanol aqueous solution, stir to dissolve, add 2.0 g of magnesium chloride, and stir for 12 hours to obtain a transparent and stable solution. The solution is concentrated by rotary evaporation to obtain a transparent spinnable gel.
[0029] b. Fiber preparation
[0030] After the above gel was left for 4 days, the filaments were picked with a glass rod to obtain composite gel filaments, dried in an oven at 100°C for 12 hours, and then calcined at 450°C to obtain magnesium oxide composite fibers.
Embodiment 3
[0032] a. Preparation of spinnable gel
[0033] Dissolve 2.0 g of polyvinylpyrrolidone in 100 mL of acetone aqueous solution, stir to dissolve, add 2.0 g of magnesium chloride, and stir for 10 hours to obtain a transparent and stable solution. The solution is concentrated by rotary evaporation to obtain a transparent spinnable gel.
[0034] b. Fiber preparation
[0035] After the above gel was left for 6 days, the filaments were picked with a glass rod to obtain composite gel filaments, dried in an oven at 100°C for 8 hours, and then calcined at 600°C to obtain magnesium oxide composite fibers.
PUM
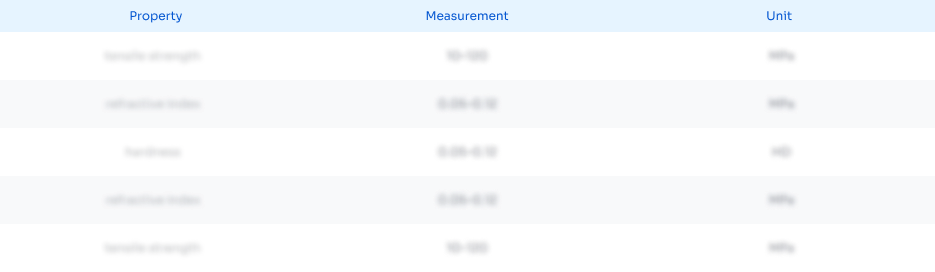
Abstract
Description
Claims
Application Information

- R&D
- Intellectual Property
- Life Sciences
- Materials
- Tech Scout
- Unparalleled Data Quality
- Higher Quality Content
- 60% Fewer Hallucinations
Browse by: Latest US Patents, China's latest patents, Technical Efficacy Thesaurus, Application Domain, Technology Topic, Popular Technical Reports.
© 2025 PatSnap. All rights reserved.Legal|Privacy policy|Modern Slavery Act Transparency Statement|Sitemap|About US| Contact US: help@patsnap.com