T iron hemming process
A process and iron-clad technology, applied in the field of T-iron forming process, can solve the problems of material waste, low efficiency, production perimeter, etc., and achieve the effects of uniform material feeding, reduction of machining costs, and improvement of production efficiency.
- Summary
- Abstract
- Description
- Claims
- Application Information
AI Technical Summary
Problems solved by technology
Method used
Image
Examples
Embodiment Construction
[0018] Embodiments of the present invention will now be described with reference to the drawings, in which like reference numerals represent like elements.
[0019] Please refer to Figure 1-3 , the T iron hemming process steps include:
[0020] (1) In the first closed cavity 11 of an indenter mold 1 , the head of an iron column 2 is hemmed and pressed to form a semi-finished product with a trapezoidal head.
[0021] (2) In the second closed cavity 31 of a flattening mold 3, the trapezoidal head of the semi-finished product formed in the above step (1) is hemmed and pressed to form a semi-finished product 4 with a straight head.
[0022] (3) In the third closed cavity 51 of a forming mold 5 , the inline head of the semi-finished product formed in the above step (2) is hemmed and pressed to form the finished product 6 .
[0023] Among them, the indenter mold 1 in step (1) includes a first upper template 12, an indenter upper mold 13, a first lower template 14, an indenter low...
PUM
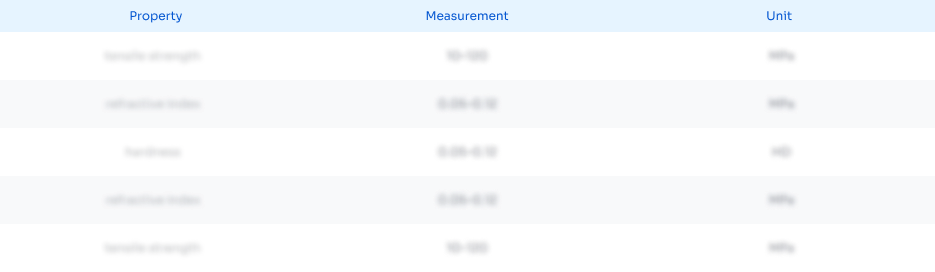
Abstract
Description
Claims
Application Information

- R&D Engineer
- R&D Manager
- IP Professional
- Industry Leading Data Capabilities
- Powerful AI technology
- Patent DNA Extraction
Browse by: Latest US Patents, China's latest patents, Technical Efficacy Thesaurus, Application Domain, Technology Topic, Popular Technical Reports.
© 2024 PatSnap. All rights reserved.Legal|Privacy policy|Modern Slavery Act Transparency Statement|Sitemap|About US| Contact US: help@patsnap.com