Temperature cascade control method of vacuum degreasing sintering furnace in metal powder injection molding
A technology of injection molding and vacuum degreasing, applied in furnace control devices, furnaces, furnace components, etc., can solve problems such as low accuracy, inability to truly display the temperature in the material box, and product performance degradation, to improve the process and improve the follow-up. Sex, the effect of shortening working hours
- Summary
- Abstract
- Description
- Claims
- Application Information
AI Technical Summary
Problems solved by technology
Method used
Image
Examples
Embodiment 1
[0028] The temperature cascade control method of metal powder injection molding vacuum degreasing sintering furnace, such as Figure 3 to Figure 6 As shown, it includes an insulating material 9, a heating element 2 and a material box 3 arranged in the sintering furnace body 1, a material plate 4 is arranged in the material box 3, a ceramic plate 17 is arranged on the material plate 4, and the product 5 is placed on the ceramic plate 17 on. It also includes a main regulator, a sub-regulator connected in series with the signal output end of the main regulator, a power controller, a first thermocouple 7 whose front end is placed inside the material box 3, and a second thermocouple whose front end is placed in the sintering furnace body 1. The pair 8 and the first thermocouple 7 are arranged on the material box 3 through the thermocouple holes opened on the wall of the material box 3, and the power controller is connected with the output end of the auxiliary regulator. The first ...
PUM
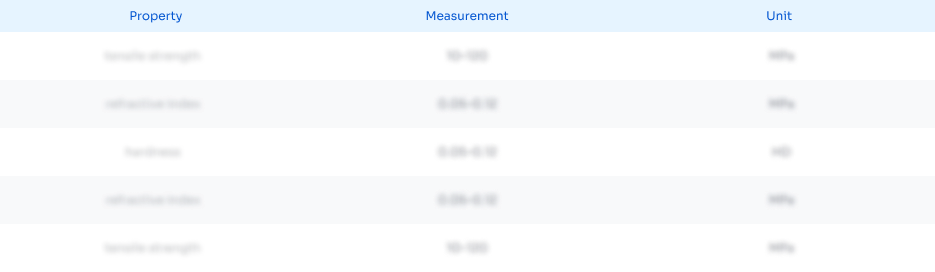
Abstract
Description
Claims
Application Information

- Generate Ideas
- Intellectual Property
- Life Sciences
- Materials
- Tech Scout
- Unparalleled Data Quality
- Higher Quality Content
- 60% Fewer Hallucinations
Browse by: Latest US Patents, China's latest patents, Technical Efficacy Thesaurus, Application Domain, Technology Topic, Popular Technical Reports.
© 2025 PatSnap. All rights reserved.Legal|Privacy policy|Modern Slavery Act Transparency Statement|Sitemap|About US| Contact US: help@patsnap.com