Aramid fiber and ultra-high molecular weight polyethylene blended yarn and production method thereof
An ultra-high molecular weight, blended yarn technology, applied in the direction of yarn, textiles and papermaking, can solve the problems of easy generation of hair balls, poor anti-pilling performance, difficult to remove hair balls, etc., to ensure yarn quality, overcome Strong rigid effect
- Summary
- Abstract
- Description
- Claims
- Application Information
AI Technical Summary
Problems solved by technology
Method used
Image
Examples
Embodiment 1
[0044] Formula: (weight percent)
[0045] Aramid fiber 85%
[0046] Ultra-high molecular weight polyethylene fiber 13%
[0047] Conductive fiber 2%
[0048] 2% antistatic agent based on the total weight of ultra-high molecular weight polyethylene fibers, aramid fibers and conductive fibers;
[0049] The yarn number is 21tex;
[0050] The ultra-high molecular weight polyethylene fiber is selected from the fiber of Sinopec Yizheng Chemical Fiber Co., Ltd., with a molecular weight between 1 million and 5 million;
[0051] Described conductive fiber is the nylon that inner core is graphite carbon, adopts the product that DuPont's trade mark is P140;
[0052] The antistatic agent is selected from the TS-YK3 antistatic agent of Dongguan Tiansheng Chemical Technology Co., Ltd.
[0053] Preparation:
[0054] (1) Raw material pretreatment:
[0055] Spray the antistatic agent evenly on the aramid fiber and ultra-high molecular weight polyethylene fiber, and let it stand for 24 ho...
Embodiment 2
[0072] formula:
[0073]
[0074] 1.5% antistatic agent based on the total weight of aramid fiber, ultra-high molecular weight polyethylene fiber, flame-retardant viscose and conductive fiber;
[0075] The yarn number is 37tex
[0076] The ultra-high molecular weight polyethylene fiber is selected from the fiber of Sinopec Yizheng Chemical Fiber Co., Ltd., with a molecular weight between 1 million and 5 million;
[0077] Described conductive fiber is the nylon that inner core is graphite carbon, adopts the product that DuPont's trade mark is P140;
[0078] The antistatic agent is selected from the TS-YK3 antistatic agent of Dongguan Tiansheng Chemical Technology Co., Ltd.
[0079] Preparation:
[0080] (1) Raw material pretreatment:
[0081] Spray antistatic agent evenly on aramid fiber, ultra-high molecular weight polyethylene, flame-retardant viscose and conductive fiber, and let it stand for 16 hours to carry out health-preserving treatment;
[0082] (2) Cotton blen...
Embodiment 3
[0097] formula:
[0098]
[0099] 2% antistatic agent based on the total weight of aramid, flame-retardant viscose fiber, ultra-high molecular weight polyethylene fiber and conductive fiber;
[0100] The yarn number is 14.6tex
[0101] The ultra-high molecular weight polyethylene fiber is selected from the fiber of Sinopec Yizheng Chemical Fiber Co., Ltd., with a molecular weight between 1 million and 5 million;
[0102] Described conductive fiber is the nylon that inner core is graphite carbon, adopts the product that DuPont's trade mark is P140;
[0103] The antistatic agent is selected from the TS-YK3 antistatic agent of Dongguan Tiansheng Chemical Technology Co., Ltd.
[0104] Preparation:
[0105] (1) Raw material pretreatment:
[0106] Spray the antistatic agent evenly on the aramid fiber, ultra-high molecular weight polyethylene, flame-retardant viscose and conductive fiber, and let it stand for 24 hours for health treatment;
[0107] (2) Cotton blending step: S...
PUM
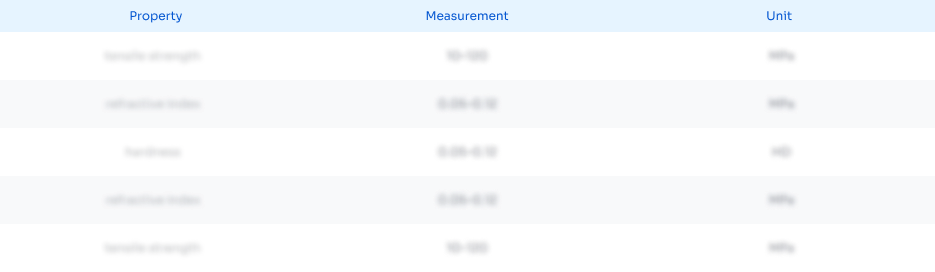
Abstract
Description
Claims
Application Information

- Generate Ideas
- Intellectual Property
- Life Sciences
- Materials
- Tech Scout
- Unparalleled Data Quality
- Higher Quality Content
- 60% Fewer Hallucinations
Browse by: Latest US Patents, China's latest patents, Technical Efficacy Thesaurus, Application Domain, Technology Topic, Popular Technical Reports.
© 2025 PatSnap. All rights reserved.Legal|Privacy policy|Modern Slavery Act Transparency Statement|Sitemap|About US| Contact US: help@patsnap.com