Cylindrical coordinate measuring machine
A measuring machine, cylindrical coordinate technology, applied in the direction of measuring devices, instruments, etc., can solve the problems of horizontality affecting the movement of the pulley body, reducing the measurement accuracy, and changing the force of the rotating shaft system.
- Summary
- Abstract
- Description
- Claims
- Application Information
AI Technical Summary
Problems solved by technology
Method used
Image
Examples
Embodiment 1
[0028] Will image 3 After the shown cast measuring cross arm 6 is installed on the rotating shaft system 1, its guide surface is processed, so that the guide surface on the first support part 601 and the second support part 602 forms an included angle with the horizontal plane of 15 " plane, and then the block body 3 is installed, and like this, the guide track to the block body 3 is formed as a straight line with a horizontal plane angle of 15 ". Verification shows that the above structure can ensure that the levelness of the movement of the tackle body 3 is within 0.1mm / 1000mm (that is, the vertical runout of the tackle body 3 is within 0.1mm for every 1000mm running of the tackle body).
Embodiment 2
[0030] Will image 3 After the shown cast measuring cross arm 6 is installed on the rotating shaft system 1, its guide surface is processed so that the guide surface on the first support part 601 and the second support part 602 forms an angle with the horizontal plane of 50 " plane, and then the block body 3 is installed, and like this, the guide track to the block body 3 is formed as a straight line with a horizontal plane angle of 50 ". Verification shows that the above structure can ensure that the levelness of the movement of the tackle body 3 is within 0.08mm / 1000mm (that is, the vertical runout of the tackle body 3 is within 0.08mm every time the tackle body 3 runs 1000mm).
Embodiment 3
[0032] Will image 3 After the shown cast measuring cross arm 6 is installed on the rotating shaft system 1, its guide surface is processed so that the guide surface on the first support part 601 and the second support part 602 forms an angle with the horizontal plane of 30 " plane, and then the block body 3 is installed, and like this, the guide track to the block body 3 is formed as a straight line with a horizontal plane angle of 30 ". Verification shows that the above structure can ensure that the levelness of the movement of the tackle body 3 is within 0.05mm / 1000mm (that is, the vertical runout of the tackle body 3 is within 0.05mm for every 1000mm running of the tackle body).
PUM
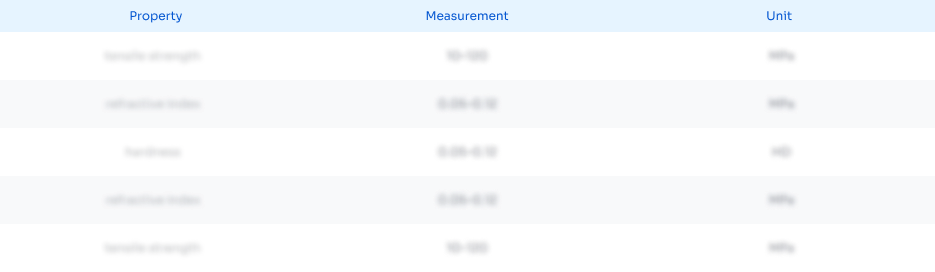
Abstract
Description
Claims
Application Information

- R&D
- Intellectual Property
- Life Sciences
- Materials
- Tech Scout
- Unparalleled Data Quality
- Higher Quality Content
- 60% Fewer Hallucinations
Browse by: Latest US Patents, China's latest patents, Technical Efficacy Thesaurus, Application Domain, Technology Topic, Popular Technical Reports.
© 2025 PatSnap. All rights reserved.Legal|Privacy policy|Modern Slavery Act Transparency Statement|Sitemap|About US| Contact US: help@patsnap.com