Middle plate bi-directional gas cutting chamfering equipment
A special equipment and chamfering technology, applied in the direction of gas flame welding equipment, welding equipment, metal processing equipment, etc., can solve the problems of unstable processing quality, high labor intensity of workers, and low processing efficiency, so as to reduce the labor intensity of workers, Elimination of safety hazards and high processing efficiency
- Summary
- Abstract
- Description
- Claims
- Application Information
AI Technical Summary
Problems solved by technology
Method used
Image
Examples
Embodiment Construction
[0011] In the figure: 1. Bracket, 2. Adjusting backing plate, 3. Positioning plate of rotating frame, 4. Guide rail of semi-automatic flame cutting machine, 5. Rotating frame, 6. GCD3-100 semi-automatic flame cutting machine, 7. Three sets of cutting torches , 8, charging positioning device.
[0012] Such as figure 1 and Figure 4 As shown, before processing the first piece of each batch of middle plates (workpiece names), (1) an adjusting backing plate 2 of corresponding thickness should be installed on the rotating frame, because the distance between the inner plane of the rotating frame and the center of rotation is 30 mm, among which When the thickness of the plate is less than 60mm, an adjusting backing plate 2 of corresponding thickness should be installed on the rotating frame (for example, when the thickness of the middle plate is 40mm, a 10mm thick adjusting backing plate should be installed), which can ensure the symmetrical mid-section and rotation of the middle pl...
PUM
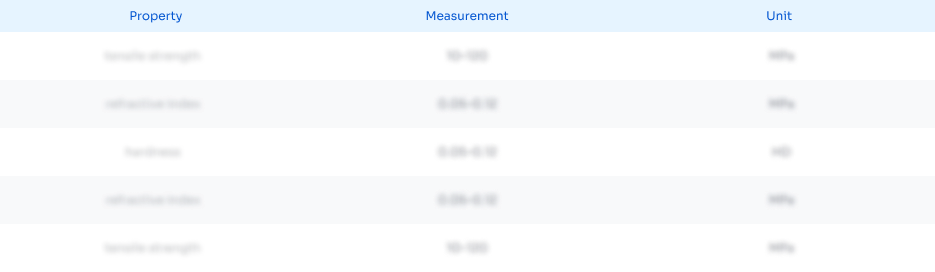
Abstract
Description
Claims
Application Information

- R&D Engineer
- R&D Manager
- IP Professional
- Industry Leading Data Capabilities
- Powerful AI technology
- Patent DNA Extraction
Browse by: Latest US Patents, China's latest patents, Technical Efficacy Thesaurus, Application Domain, Technology Topic, Popular Technical Reports.
© 2024 PatSnap. All rights reserved.Legal|Privacy policy|Modern Slavery Act Transparency Statement|Sitemap|About US| Contact US: help@patsnap.com