Device for testing axial bearing capacity of conical dynamic-pressure spiral groove bearing
A test device and load-carrying capacity technology, which is applied in the direction of mechanical bearing testing, etc., to achieve the effects of simple testing, solving impact loads, and reducing system vibration
- Summary
- Abstract
- Description
- Claims
- Application Information
AI Technical Summary
Problems solved by technology
Method used
Image
Examples
Embodiment Construction
[0018] Structurally, the test device for the axial bearing capacity of the conical dynamic pressure spiral groove bearing consists of a mechanical part and an electric control part. The mechanical part includes: test device frame, transmission shaft, bearing seat ring, washer, damping ring, loading sleeve, split positioning ring, ball, loading lever, strain beam; the electronic control part includes: frequency converter, high frequency motor, Dynamic and static strain gauges.
[0019] The high-frequency motor is installed on the upper part of the test device frame, connected with the frequency converter, and the test bearing is connected with the motor shaft. The test housing is located inside the bearing race. The bearing race is located under the drive shaft and fits inside the damping ring. The damping ring is located between the bearing load sleeve and the bearing race. A U-shaped groove is opened in the loading sleeve, and the strain beam is embedded in it. The gasket...
PUM
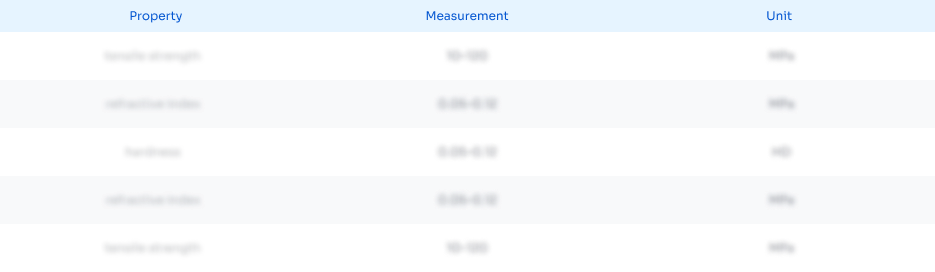
Abstract
Description
Claims
Application Information

- R&D
- Intellectual Property
- Life Sciences
- Materials
- Tech Scout
- Unparalleled Data Quality
- Higher Quality Content
- 60% Fewer Hallucinations
Browse by: Latest US Patents, China's latest patents, Technical Efficacy Thesaurus, Application Domain, Technology Topic, Popular Technical Reports.
© 2025 PatSnap. All rights reserved.Legal|Privacy policy|Modern Slavery Act Transparency Statement|Sitemap|About US| Contact US: help@patsnap.com