Wing load applying device for large aircraft strength test
A technology of aircraft strength and application device, which is applied in the field of aviation fatigue test, can solve the problems of long fatigue test cycle, affecting the load balance of the whole aircraft, and slow loading speed, so as to improve the accuracy of loading and assessment, avoid distortion of assessment, and reduce difficulty Effect
- Summary
- Abstract
- Description
- Claims
- Application Information
AI Technical Summary
Problems solved by technology
Method used
Image
Examples
Embodiment Construction
[0012] Below in conjunction with accompanying drawing the present invention is described in further detail, please refer to figure 1 and figure 2 .
[0013] Such as figure 1 Shown is a schematic diagram of the structure of the present invention.
[0014] A large-scale aircraft strength test wing load application device, including a pillar system 1, a loading platform 2, several platform moving actuators 3 and several loading actuators 4, the loading platform 2 consists of a tripod 201 and a flat plate 202 The other end of the triangular bracket 201 is hinged on the pillar system 1, and several platform moving actuators 3 are hinged on the triangular bracket 201, and the other end of the platform moving actuator 3 is hinged on the pillar system 1. One end of the several loading cylinders 4 is hinged on the loading platform 2, and the other end is hinged on the wing 5.
[0015] The pillar system 1 is composed of more than two triangular pillars 101 and crossbeams 102 , and ...
PUM
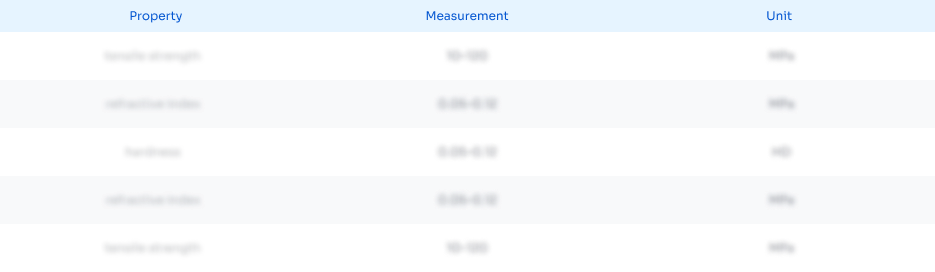
Abstract
Description
Claims
Application Information

- R&D
- Intellectual Property
- Life Sciences
- Materials
- Tech Scout
- Unparalleled Data Quality
- Higher Quality Content
- 60% Fewer Hallucinations
Browse by: Latest US Patents, China's latest patents, Technical Efficacy Thesaurus, Application Domain, Technology Topic, Popular Technical Reports.
© 2025 PatSnap. All rights reserved.Legal|Privacy policy|Modern Slavery Act Transparency Statement|Sitemap|About US| Contact US: help@patsnap.com