Forming method capable of guaranteeing quality of chemically-milled thick skin workpieces
A technology of skinning and parts, applied in the field of aviation technology, can solve the problems of increased production cost, high cost, and small pre-stretched plate specifications, and achieve the effects of reducing hardening performance, good plasticity, and improving forming quality
- Summary
- Abstract
- Description
- Claims
- Application Information
AI Technical Summary
Problems solved by technology
Method used
Image
Examples
Embodiment Construction
[0016] Such as figure 1 As shown, a forming method to ensure the quality of chemically milled thick skin parts includes the following specific steps:
[0017] (1) Choose an aluminum alloy non-pre-stretched plate or a titanium alloy non-pre-stretched plate to make the skin blank. During production, it is necessary to reserve jaw clamping margins in the two jaw directions 2 of the skin blank 1 according to the size of the part. The clamping margin is specifically: the width is 45mm, and the length is equal to the length of the skin blank 1;
[0018] (2) Prepare 4 craft aluminum strips 3. The craft aluminum strip 3 adopts LY12. Since the size of the craft aluminum strip needs to be consistent with the clamping margin reserved in the jaw direction, the width of the craft aluminum strip 3 is 45mm , the thickness is 1.2mm, and the length is also equal to the length of the skin blank 1;
[0019] (3) If the skin blank 1 is an aluminum alloy non-pre-stretched plate, use phosphoric ac...
PUM
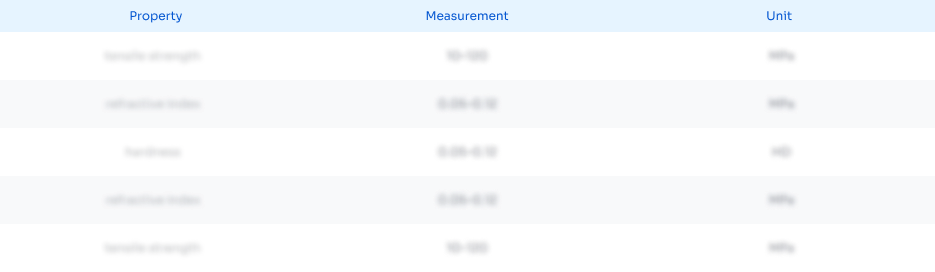
Abstract
Description
Claims
Application Information

- Generate Ideas
- Intellectual Property
- Life Sciences
- Materials
- Tech Scout
- Unparalleled Data Quality
- Higher Quality Content
- 60% Fewer Hallucinations
Browse by: Latest US Patents, China's latest patents, Technical Efficacy Thesaurus, Application Domain, Technology Topic, Popular Technical Reports.
© 2025 PatSnap. All rights reserved.Legal|Privacy policy|Modern Slavery Act Transparency Statement|Sitemap|About US| Contact US: help@patsnap.com