Mirror driving device and method of controlling the device
一种驱动设备、驱动电压的技术,应用在光学、仪器、电气元件等方向,能够解决影响、结构扰动、谐振频率低等问题,达到谐振频率高、快速响应、干扰振动的影响抑制的效果
- Summary
- Abstract
- Description
- Claims
- Application Information
AI Technical Summary
Problems solved by technology
Method used
Image
Examples
no. 1 example
[0058] figure 1 is a plan view of the MEMS scanner device according to the first embodiment. figure 2 yes figure 1 A partially enlarged view of . image 3 is schematically depicted figure 1 A diagram of the device structure. As depicted in these figures, a MEMS scanner device 10 (corresponding to a "mirror drive device") according to the present embodiment includes: a mirror part 12; two actuators 14 and 24 surrounding this mirror part 12; and a support The frame 30 of these actuators 14 and 24 is fixed. At diagonal positions of the mirror member 12, mirror support members 15 and 25 are formed. The actuators 14 and 24 have one end connected to the mirror support members 15 and 25 and the other end fixed to a fixed part, the fixed parts being denoted by reference numerals 31 and 32, respectively.
[0059] The mirror member 12 in this example has a substantially rectangular shape in plan view. On the mirror surface (upper surface of mirror member 12 ) serving as refle...
no. 2 example
[0151] Figure 19 is a schematic diagram of the structure of the MEMS scanner device according to the second embodiment. exist Figure 19 in, give Figure 1 to Figure 3 The same or similar elements as those in the structure of the first embodiment described in are given the same reference numerals and will not be described here.
[0152] and image 3 Compared with the structure of Figure 19 In the structure depicted in , the connection sequence of the piezoelectric cantilever in the first actuator 14 and the second actuator 24 is changed. Such as Figure 19 As depicted in , the piezoelectric cantilevers 16-1 and 16-2 for x-axis rotation in this first actuator 14 are connected together via a coupling member 19-3 to be folded to the y-axis direction, and the piezoelectric cantilever 16 -2 and a piezoelectric cantilever 17 - 1 for y-axis rotation are connected together via a coupling member 19 - 4 , and one end of the piezoelectric cantilever 17 - 2 is connected to the mir...
PUM
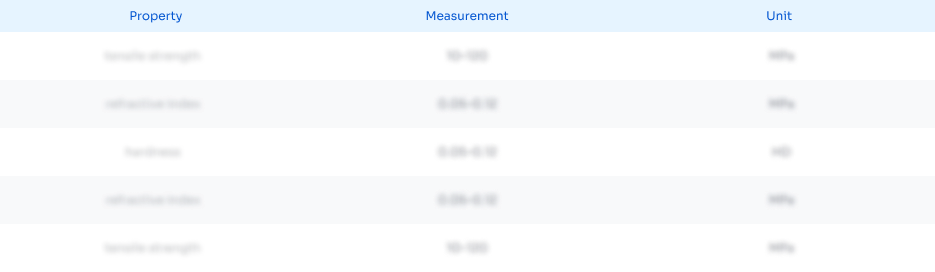
Abstract
Description
Claims
Application Information

- R&D
- Intellectual Property
- Life Sciences
- Materials
- Tech Scout
- Unparalleled Data Quality
- Higher Quality Content
- 60% Fewer Hallucinations
Browse by: Latest US Patents, China's latest patents, Technical Efficacy Thesaurus, Application Domain, Technology Topic, Popular Technical Reports.
© 2025 PatSnap. All rights reserved.Legal|Privacy policy|Modern Slavery Act Transparency Statement|Sitemap|About US| Contact US: help@patsnap.com