Method for on-line monitoring and alarming of convection heating face flue gas temperature field of power station boiler
A technology for flue gas temperature and power station boilers, which is used in the indication of boiler working conditions, lighting and heating equipment, control systems, etc. Boiler operating pressure and temperature increase, to achieve the effect of extending service life, ensuring safe and economical operation, and eliminating pipe bursts
- Summary
- Abstract
- Description
- Claims
- Application Information
AI Technical Summary
Problems solved by technology
Method used
Image
Examples
Embodiment 1
[0070] In this embodiment, the inlet plane of the final superheater of a 1036MW ultra-supercritical boiler in a power plant is selected as an embodiment. use figure 1 The block schematic diagram of the implementation steps is shown.
[0071] This embodiment includes the following steps:
[0072] Step 1: According to the monitoring of the dynamic metal wall temperature in the convection heating surface furnace of the utility boiler, obtain the monitoring values of the furnace inner wall temperature at each point on the inlet and outlet planes of the heating surface, and calculate the average value of the furnace inner wall temperature on the inlet and outlet planes;
[0073] This embodiment calculates the import through the existing technology (Chinese patent document number: CN102494325A, publication date: 2012-06-13, named: method for monitoring dynamic wall temperature in the high-temperature tube system of power plant boiler, etc.) The average temperature of the inner wal...
PUM
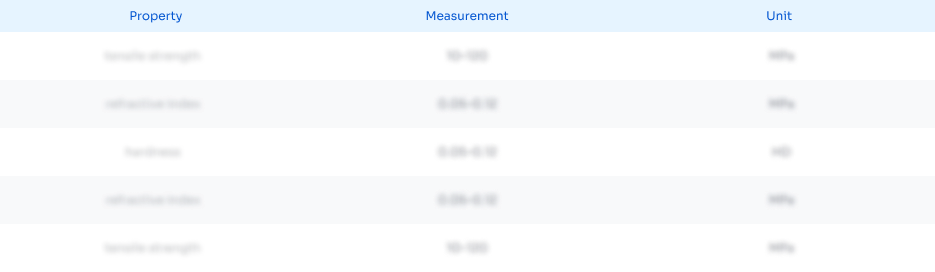
Abstract
Description
Claims
Application Information

- R&D Engineer
- R&D Manager
- IP Professional
- Industry Leading Data Capabilities
- Powerful AI technology
- Patent DNA Extraction
Browse by: Latest US Patents, China's latest patents, Technical Efficacy Thesaurus, Application Domain, Technology Topic, Popular Technical Reports.
© 2024 PatSnap. All rights reserved.Legal|Privacy policy|Modern Slavery Act Transparency Statement|Sitemap|About US| Contact US: help@patsnap.com