Special washing branding discoloration resin for synthetic leather and preparation method thereof
A synthetic leather and resin technology, applied in textiles and papermaking, etc., can solve the problems of single color and surface pattern, insufficient burnt feeling of branded parts, poor wear resistance and scratch resistance, etc., and achieve good discoloration effect, good visual effect, durable Good abrasion and scratch resistance
- Summary
- Abstract
- Description
- Claims
- Application Information
AI Technical Summary
Problems solved by technology
Method used
Examples
Embodiment 1
[0031] Mix 30 parts of polyurethane resin, 28 parts of N,N-dimethylformamide and 30 parts of butyl acetate in the kettle, and then add 1 part of epoxy soybean oil and 2 parts of silicone while stirring. Mixing agent, 1 part of silica matting powder and 8 parts of micronized wax powder, stir for 30min to make it completely dispersed. The viscosity measured by sampling is 1200cps / 25℃, and the product is filtered and discharged.
[0032] After adding 3% color paste to the prepared water-washed branding and color-changing resin, it is applied to the surface of dry synthetic leather by roller coating, dried at 130°C, kneaded in water for 30 minutes, and taken out for drying. Then use a branding machine to brand the surface to obtain a branded and color-changing synthetic leather with a clear pattern.
Embodiment 2
[0034] Stir 35 parts of polyurethane resin, 40 parts of N,N-dimethylformamide and 12.5 parts of butyl acetate in the kettle, and then add 0.5 parts of epoxy fatty acid methyl ester and 1 part of silicone while stirring. Hand-feeling agent, 3 parts of silicon dioxide matting powder and 8 parts of micronized wax powder, stir for 30 minutes to make it completely dispersed. The viscosity measured by sampling is 2000cps / 25℃, and the product is filtered and discharged.
[0035] After adding 3% color paste to the prepared water-washed branding and color-changing resin, it is coated on the surface of dry synthetic leather by roller coating, dried at 130°C, kneaded in water for 30 minutes, and taken out for drying. Then use a branding machine to brand the surface to obtain a branded and color-changing synthetic leather with a clear pattern.
Embodiment 3
[0037] Stir 40 parts of polyurethane resin, 30 parts of N,N-dimethylformamide and 14.5 parts of butyl acetate in the kettle, and then add 1 part of epoxy fatty acid methyl ester and 0.5 parts of silicone while stirring. Feeling agent, 2 parts of silicon dioxide matting powder and 12 parts of micronized wax powder, stir for 30 minutes to make it completely dispersed. The viscosity measured by sampling is 3000cps / 25℃, and the product is filtered and discharged.
[0038] After adding 5% color paste to the prepared water-washed branding color-changing resin, it is pasted on the surface of wet synthetic leather with release paper veneer, dried at 130°C, kneaded in water for 30 minutes, and taken out for drying. Then use a branding machine to brand the surface to obtain a branded and color-changing synthetic leather with a clear pattern.
PUM
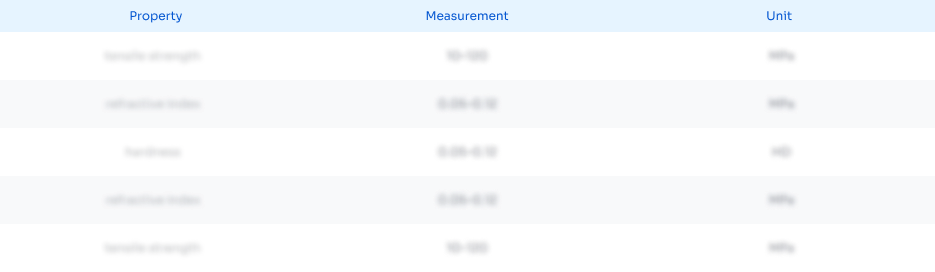
Abstract
Description
Claims
Application Information

- Generate Ideas
- Intellectual Property
- Life Sciences
- Materials
- Tech Scout
- Unparalleled Data Quality
- Higher Quality Content
- 60% Fewer Hallucinations
Browse by: Latest US Patents, China's latest patents, Technical Efficacy Thesaurus, Application Domain, Technology Topic, Popular Technical Reports.
© 2025 PatSnap. All rights reserved.Legal|Privacy policy|Modern Slavery Act Transparency Statement|Sitemap|About US| Contact US: help@patsnap.com