An online self-calibration method for angular displacement sensor
A technology of angular displacement sensor and sensor, which is applied in the direction of instruments, measuring devices, and electrical devices, etc., can solve problems such as discomfort, and achieve the effect of fewer sampling points
- Summary
- Abstract
- Description
- Claims
- Application Information
AI Technical Summary
Problems solved by technology
Method used
Image
Examples
Embodiment Construction
[0041] The technical solution of the present invention will be described in further detail below in conjunction with the accompanying drawings.
[0042] see figure 1 , an error online self-calibration method of an angular displacement sensor system is: in a magnetic grating sensor composed of a main reading head 1, an auxiliary reading head 2, a magnetic disk 3, a rotor 4 and a stator 5, the magnetic disk 3 is fixed on the stator 5, The main reading head 1 is fixed on the rotor 4 and rotates with the measured object, and the auxiliary reading head 2 can be fixed with the rotor 4 or the stator 5; the main reading head 1 can read the disk to realize the angular displacement of the measured object Measurement; the auxiliary reading head 2 can also read the disk, and the rotor can be rotated under the indication of the auxiliary reading head 2, so that a fixed special angle relative movement can be realized between the sensor rotor and the stator. In this embodiment, the auxiliary...
PUM
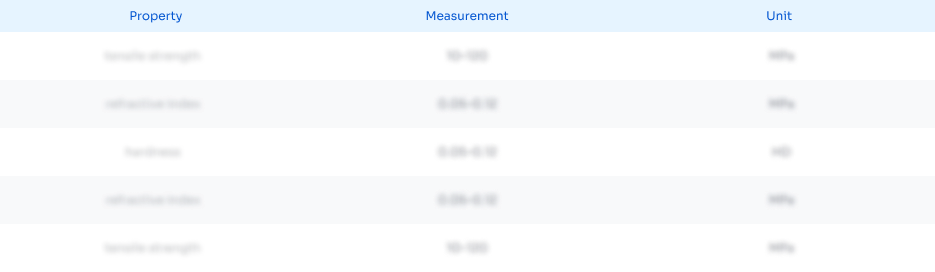
Abstract
Description
Claims
Application Information

- Generate Ideas
- Intellectual Property
- Life Sciences
- Materials
- Tech Scout
- Unparalleled Data Quality
- Higher Quality Content
- 60% Fewer Hallucinations
Browse by: Latest US Patents, China's latest patents, Technical Efficacy Thesaurus, Application Domain, Technology Topic, Popular Technical Reports.
© 2025 PatSnap. All rights reserved.Legal|Privacy policy|Modern Slavery Act Transparency Statement|Sitemap|About US| Contact US: help@patsnap.com