Quick curing processing technology for composite material
A processing technology and composite material technology, applied in chemical instruments and methods, lamination devices, lamination auxiliary operations, etc., can solve problems such as low curing rate, unfavorable solvent volatilization, direct conduction of hot air, unfavorable high-efficiency production, etc., to achieve The effect of increasing the ripening rate
- Summary
- Abstract
- Description
- Claims
- Application Information
AI Technical Summary
Problems solved by technology
Method used
Image
Examples
Embodiment Construction
[0018] The technical solution of the present invention will be further described below in conjunction with a preferred embodiment and the accompanying drawings.
[0019] Aiming at the aforementioned shortcomings of the traditional process, this embodiment aims to provide a processing technology that can rapidly ripen the composite material membrane, see Figure 2-Figure 3 , its technical solutions include:
[0020] A rewinding shaft 2 is provided, and a baffle frame 3 is sleeved at both ends of the rewinding shaft;
[0021] And, utilize described winding shaft to wind up the composite material film 1 with multi-layer structure, and in the winding process (according to figure 2 Rotate in the direction indicated by the arrow in the center), so that the two ends of the composite material film are in contact with the concave-convex texture structure distributed radially on the inside of the baffle frame, due to the blocking friction provided by the concave-convex texture, the fo...
PUM
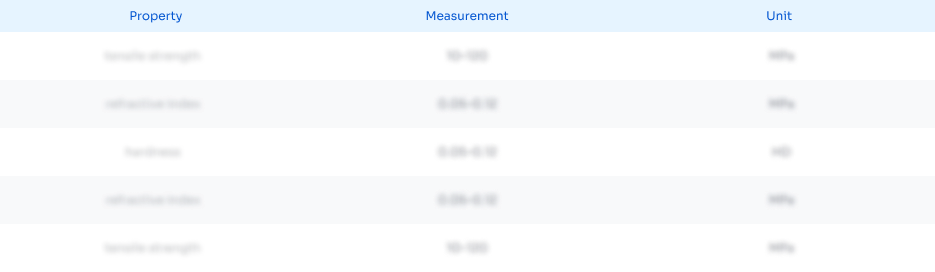
Abstract
Description
Claims
Application Information

- R&D Engineer
- R&D Manager
- IP Professional
- Industry Leading Data Capabilities
- Powerful AI technology
- Patent DNA Extraction
Browse by: Latest US Patents, China's latest patents, Technical Efficacy Thesaurus, Application Domain, Technology Topic, Popular Technical Reports.
© 2024 PatSnap. All rights reserved.Legal|Privacy policy|Modern Slavery Act Transparency Statement|Sitemap|About US| Contact US: help@patsnap.com