Ejection mechanism for internal inverted buckle in injection mould
A technology of internal undercut and demoulding mechanism, which is applied in the field of injection molds and can solve problems affecting injection molding, product scrapping, and product quality
- Summary
- Abstract
- Description
- Claims
- Application Information
AI Technical Summary
Problems solved by technology
Method used
Image
Examples
Embodiment Construction
[0011] The present invention relates to an internal buckle release mechanism of an injection mold, such as figure 1 — Figure 4 As shown, it includes the upper doubler plate 1 and the lower doubler plate 2, the positioning ring 3 is installed in the upper doubler plate, the cavity 4 is installed under the upper doubler plate, the perforation 5 is opened in the lower doubler plate 2, and the die foot 6 is installed on the lower doubler plate , there is a swing rod installation groove 7 in the mold foot, a swing rod 8 is installed in the swing rod installation groove, the swing rod is connected with the mold foot 6 through a pin shaft 9, a support plate 10 is installed on the mold foot 6, and the support plate is installed Core insert 11 and core fixing plate 12, stripping plate 13 is installed on the core fixing plate, plastic product 14 is arranged between stripping plate, core insert 11 and cavity 4, and the middle part of the plastic product is formed with internal Undercut...
PUM
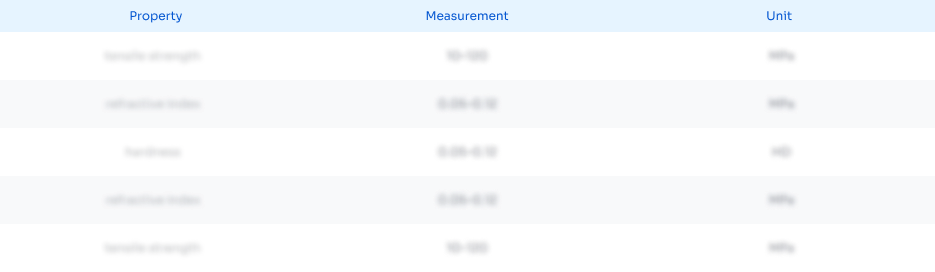
Abstract
Description
Claims
Application Information

- R&D
- Intellectual Property
- Life Sciences
- Materials
- Tech Scout
- Unparalleled Data Quality
- Higher Quality Content
- 60% Fewer Hallucinations
Browse by: Latest US Patents, China's latest patents, Technical Efficacy Thesaurus, Application Domain, Technology Topic, Popular Technical Reports.
© 2025 PatSnap. All rights reserved.Legal|Privacy policy|Modern Slavery Act Transparency Statement|Sitemap|About US| Contact US: help@patsnap.com