Hull without stern cover and unbalanced rudder blade
A stern seal and unbalanced technology, which is applied to the hull, hull parts, rudder steering, etc., can solve the problems of increased scissors gap and reduced rudder effect, so as to improve maneuverability, improve rudder effect, and improve rudder efficiency. effective effect
- Summary
- Abstract
- Description
- Claims
- Application Information
AI Technical Summary
Problems solved by technology
Method used
Image
Examples
Embodiment Construction
[0015] The present invention will be further described below in conjunction with the accompanying drawings and specific embodiments.
[0016] figure 1 It is a side view (straight sectional view) of the present invention, showing the relative position of the rudder and the hull when part of the straight section line and the rudder are at a rudder angle of 0°;
[0017] figure 2 It is the A-direction view (station plan) of the present invention, due to symmetry, only part of the molded line on the port side is shown;
[0018] image 3 It is a B-direction view (waterline view) of the present invention. Due to symmetry, only part of the molded line on the port side is shown.
[0019] During specific implementation, obtain a satisfactory hull shape line according to the following steps. like figure 1 As shown, the curve segment oa is intercepted on the 0° straight profile line 4a of the hull as the generatrix 7 of the hull spiral surface.
[0020] 1. Taking the busbar 7 of th...
PUM
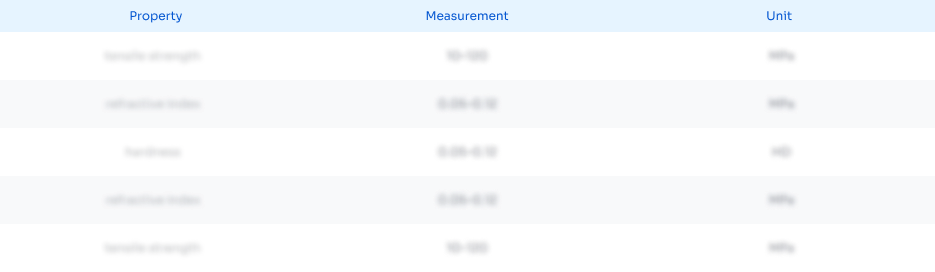
Abstract
Description
Claims
Application Information

- Generate Ideas
- Intellectual Property
- Life Sciences
- Materials
- Tech Scout
- Unparalleled Data Quality
- Higher Quality Content
- 60% Fewer Hallucinations
Browse by: Latest US Patents, China's latest patents, Technical Efficacy Thesaurus, Application Domain, Technology Topic, Popular Technical Reports.
© 2025 PatSnap. All rights reserved.Legal|Privacy policy|Modern Slavery Act Transparency Statement|Sitemap|About US| Contact US: help@patsnap.com