Compact electric servo mechanism for linear displacement
A linear displacement, electric servo technology, applied in the field of servo mechanisms, can solve the problems of difficult assembly of long threaded holes, increase the difficulty of motor design, destroy the integrity of the motor structure, etc., to reduce the transmission clearance and system inertia, The effect of reducing design difficulty and improving connection accuracy
- Summary
- Abstract
- Description
- Claims
- Application Information
AI Technical Summary
Problems solved by technology
Method used
Image
Examples
Embodiment Construction
[0028] The present invention realizes the direct drive form by adopting the roller screw pair, no intermediate transmission link is needed, the output shaft of the motor is directly connected with the ball screw, and the rotational speed of the motor directly drives the ball screw to rotate. During the rotation, the self-aligning roller The sub-bearing is fixed on the driving end of the roller screw, so that the motor shaft and the ball screw are automatically adjusted during the rotation. The ball screw drives the screw nut to move through the screw rollers. Since the guide effectively constrains the rotational movement of the ball screw nut, the precise linear motion of the ball screw nut is realized. The present invention will be described in detail below in conjunction with the accompanying drawings and specific examples.
[0029] The present invention as figure 2 As shown, it includes support seat 1, sliding bearing 2, motor connector 3, motor 4, motor housing 5, spheri...
PUM
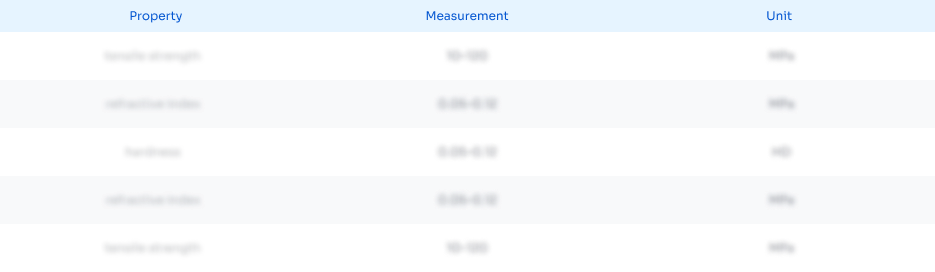
Abstract
Description
Claims
Application Information

- R&D
- Intellectual Property
- Life Sciences
- Materials
- Tech Scout
- Unparalleled Data Quality
- Higher Quality Content
- 60% Fewer Hallucinations
Browse by: Latest US Patents, China's latest patents, Technical Efficacy Thesaurus, Application Domain, Technology Topic, Popular Technical Reports.
© 2025 PatSnap. All rights reserved.Legal|Privacy policy|Modern Slavery Act Transparency Statement|Sitemap|About US| Contact US: help@patsnap.com