Connecting rod type synergy drive robot finger
A robotic finger and connecting rod technology, applied in the direction of manipulators, joints, chucks, etc., can solve the problems of fast grasping speed, excessive energy loss, and failure to reach, and achieve precise grasping action, large grasping force, and fast The effect of grasping speed
- Summary
- Abstract
- Description
- Claims
- Application Information
AI Technical Summary
Problems solved by technology
Method used
Image
Examples
Embodiment Construction
[0026] The specific structure and working principle of the present invention will be further described in detail below in conjunction with the accompanying drawings and embodiments.
[0027] An embodiment of the double-joint co-direction transmission composite underactuated robot finger device of the present invention, as Figure 1 to Figure 5a , 5b, including the first screw motor 1, the base 2, the middle finger section 6, the proximal joint shaft 7, the distal joint shaft 16 and the end finger section 17; the first screw motor 1 is installed on the base 2 Above, the proximal joint shaft 7 is sleeved in the base 2, the distal joint shaft 16 is sleeved in the middle finger segment 6, and the middle finger segment 6 is sleeved on the proximal joint shaft 7; the terminal finger segment 17 Sleeved on the distal joint shaft 16; it is characterized in that: the device also includes a first nut slider 3, a first connecting rod 5, a second connecting rod 8, a second screw motor 9, a...
PUM
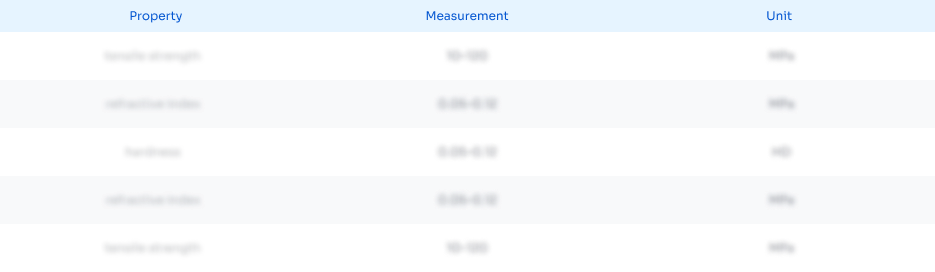
Abstract
Description
Claims
Application Information

- Generate Ideas
- Intellectual Property
- Life Sciences
- Materials
- Tech Scout
- Unparalleled Data Quality
- Higher Quality Content
- 60% Fewer Hallucinations
Browse by: Latest US Patents, China's latest patents, Technical Efficacy Thesaurus, Application Domain, Technology Topic, Popular Technical Reports.
© 2025 PatSnap. All rights reserved.Legal|Privacy policy|Modern Slavery Act Transparency Statement|Sitemap|About US| Contact US: help@patsnap.com