Process for manufacturing a part made of a composite having a hollow core
A technology of synthetic materials and cores, applied to objects with hollow walls, household appliances, and other household appliances, etc., can solve the problems of complex and large-scale manufacturing methods, and achieve the effect of improving mechanical properties
- Summary
- Abstract
- Description
- Claims
- Application Information
AI Technical Summary
Problems solved by technology
Method used
Image
Examples
Embodiment Construction
[0058] figure 1 The manufacture of a sealed hollow-cell honeycomb core 1 for the manufacture of composite material parts is shown.
[0059] To this end, the honeycomb core 1 is placed on a mold 2 and covered by a semi-rigid film 3 which forms a counter-mold and is associated with a device 4 for matching the mold 2 and the semi-rigid A vacuum is applied to the inner space defined by the membrane 3 .
[0060] The vacuum applied may typically be a vacuum of less than 100 mbar, and preferably a vacuum of greater than 4 mbar.
[0061] The semi-rigid membrane 3 can be, for example, a silicone membrane.
[0062] Gasket 5 ensures the seal between semi-rigid membrane 3 and mold 2 .
[0063] According to the invention, the honeycomb core 3 has upper and lower open surfaces covered with a polymerizable adhesive film 6, in particular of the epoxy adhesive type.
[0064]Preferably, the polymerizable adhesive film 6 is supported, ie reinforced, by weft threads, in particular by glass fi...
PUM
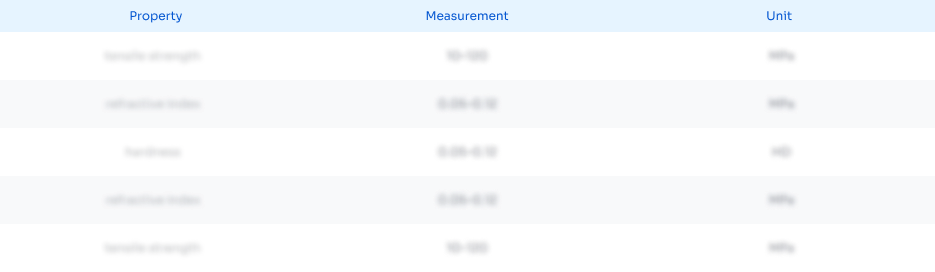
Abstract
Description
Claims
Application Information

- R&D
- Intellectual Property
- Life Sciences
- Materials
- Tech Scout
- Unparalleled Data Quality
- Higher Quality Content
- 60% Fewer Hallucinations
Browse by: Latest US Patents, China's latest patents, Technical Efficacy Thesaurus, Application Domain, Technology Topic, Popular Technical Reports.
© 2025 PatSnap. All rights reserved.Legal|Privacy policy|Modern Slavery Act Transparency Statement|Sitemap|About US| Contact US: help@patsnap.com