Loading system for multiple vehicle frames
A multi-model and frame technology, applied in the field of the upper part system of the multi-model frame, can solve the problems of not being able to be placed directly, increasing the system design amount, and wasting loading time, so as to save costs, reduce complexity and reduce consumption. , the effect of improving production efficiency
- Summary
- Abstract
- Description
- Claims
- Application Information
AI Technical Summary
Problems solved by technology
Method used
Image
Examples
Embodiment Construction
[0027] like figure 1 As shown, the multi-model frame loading system includes: spreader trolley, track, trolley line, chain, ground mobile trolley, frequency conversion motor, steel structure (network protection, maintenance platform, main frame), operation platform, electric control system composition. It is characterized in that: a positioning mechanism that cooperates with the spreader is set at the loading point and the unloading point.
[0028] The traveling speed of the spreader trolley is driven by frequency conversion, and the conveying speed is 5m / min-20m / min.
[0029] The spreader trolley adopts stepless frequency conversion speed regulation.
[0030] The hoisting mechanism of the spreader trolley adopts the motor-driven four-chain hoisting form.
[0031] The lifting speed of the spreader is driven by frequency conversion, and the conveying speed is 2 m / min-15 m / min; stepless frequency conversion speed regulation.
[0032] The hoisting height of the spreader troll...
PUM
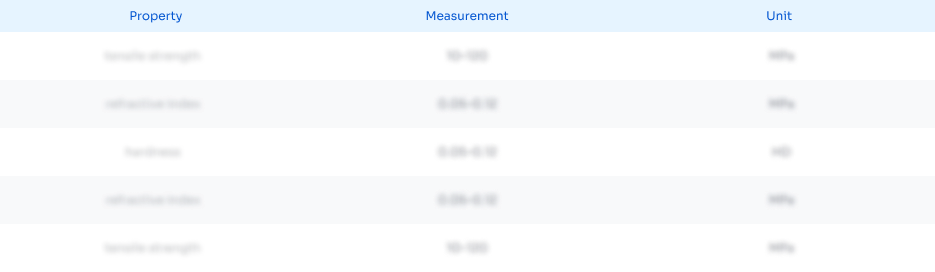
Abstract
Description
Claims
Application Information

- R&D
- Intellectual Property
- Life Sciences
- Materials
- Tech Scout
- Unparalleled Data Quality
- Higher Quality Content
- 60% Fewer Hallucinations
Browse by: Latest US Patents, China's latest patents, Technical Efficacy Thesaurus, Application Domain, Technology Topic, Popular Technical Reports.
© 2025 PatSnap. All rights reserved.Legal|Privacy policy|Modern Slavery Act Transparency Statement|Sitemap|About US| Contact US: help@patsnap.com