Automotive carpet walk-in forming equipment
A technology for automobile carpets and molding equipment, which is applied in the directions of lamination device, lamination auxiliary operation, lamination, etc., can solve the problems of incorrect orientation, high manufacturing cost, long connection movement distance, etc., achieves accurate and convenient positioning and cutting, and reduces labor costs. The effect of high labor intensity and equipment safety
- Summary
- Abstract
- Description
- Claims
- Application Information
AI Technical Summary
Problems solved by technology
Method used
Image
Examples
Embodiment Construction
[0017] Below the present invention will be further described in conjunction with the embodiment in the accompanying drawing:
[0018] As shown in the figure, the automobile carpet walk-in forming equipment in the embodiment mainly includes several parts of a feeding trolley 25, a feeding mechanism, a feeding heating mechanism and a forming mechanism; the feeding trolley 25 is used for laying sheet raw materials, Form the sheet carpet, and the feeding mechanism is used to take out the sheet carpet laid on the feeding trolley 25 and transport it to the feeding heating mechanism, and the feeding heating mechanism is used to heat the sheet carpet and transport it to the forming Mechanism, the forming mechanism is used to press and shape the heated sheet carpet and cooperate with manual cutting.
[0019] Such as figure 1 , figure 2 As shown, the feeding mechanism is installed on the overall frame 26, and the feeding mechanism is mainly composed of carpet acupuncture 11, carpet ...
PUM
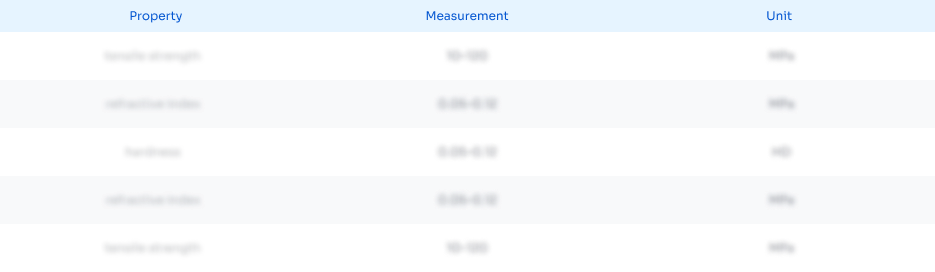
Abstract
Description
Claims
Application Information

- R&D
- Intellectual Property
- Life Sciences
- Materials
- Tech Scout
- Unparalleled Data Quality
- Higher Quality Content
- 60% Fewer Hallucinations
Browse by: Latest US Patents, China's latest patents, Technical Efficacy Thesaurus, Application Domain, Technology Topic, Popular Technical Reports.
© 2025 PatSnap. All rights reserved.Legal|Privacy policy|Modern Slavery Act Transparency Statement|Sitemap|About US| Contact US: help@patsnap.com