Welding method for use in high-quality steel continuous rolling
A welding method and high-quality steel technology, applied in welding equipment, arc welding equipment, manufacturing tools, etc., can solve problems such as troublesome operation, broken belts, and restrictions on enterprise development, and achieve the effects of low cost, convenient use, and simple operation
- Summary
- Abstract
- Description
- Claims
- Application Information
AI Technical Summary
Problems solved by technology
Method used
Image
Examples
Embodiment Construction
[0025] use figure 1 The two high-quality steel strips to be welded are illustrated, and the welding methods for continuous rolling of high-quality steel include:
[0026] 1) Perform an annealing process on the high-quality steel strip to be welded before welding;
[0027] 2) Put the tail end of the first high-quality steel strip 1 fed into the spiral looper device and the head end of the second high-quality steel strip 2 that has just been sent to the frame material on the welding platform;
[0028] 3) Use the pressure plate on the welding platform to press the end of the high-quality steel strip to ensure that the steel strip will not move;
[0029] 4) Utilize the injection-suction cutting torch to uniformly heat the heating area 3 at the end of the two high-quality steel strips, and at the same time, heat the end faces of the first high-quality steel strip 1 and the second high-quality steel strip 2 Heating back and forth to ensure uniform heating;
[0030] 5) Use argon a...
PUM
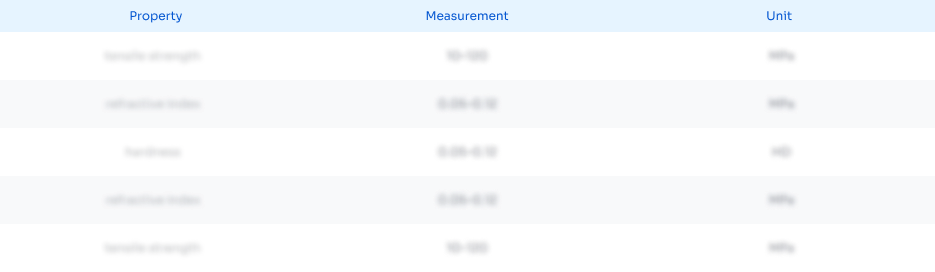
Abstract
Description
Claims
Application Information

- R&D
- Intellectual Property
- Life Sciences
- Materials
- Tech Scout
- Unparalleled Data Quality
- Higher Quality Content
- 60% Fewer Hallucinations
Browse by: Latest US Patents, China's latest patents, Technical Efficacy Thesaurus, Application Domain, Technology Topic, Popular Technical Reports.
© 2025 PatSnap. All rights reserved.Legal|Privacy policy|Modern Slavery Act Transparency Statement|Sitemap|About US| Contact US: help@patsnap.com