Air entraining structure of engine
A technology of engine and air bleed holes, which is applied in the direction of engine cooling, engine components, machine/engine, etc., can solve the problem of inability to cool down the hot end components, and achieves lower temperature, improved service life and reliability, and good diversion effect. Effect
- Summary
- Abstract
- Description
- Claims
- Application Information
AI Technical Summary
Problems solved by technology
Method used
Image
Examples
Embodiment Construction
[0020] The embodiments of the present invention will be described in detail below with reference to the accompanying drawings, but the present invention can be implemented in many different ways defined and covered by the claims.
[0021] see figure 1 , The bleed air structure of the engine of the present invention is applied to an aero-engine. The engine includes an inner rotating shaft 1 , a compressor axial flow rotor 2 and a centrifugal impeller 3 . The compressor axial flow rotor 2 and the centrifugal impeller 3 are coaxially and fixedly installed on the inner rotating shaft 1 . A gap 4 is formed between the opposite end surfaces of the compressor axial flow rotor 2 and the centrifugal impeller 3 , and the gap 4 communicates with external cold air. The inner wall surface of one end of the compressor axial flow rotor 2 adjacent to the centrifugal impeller 3 is radially provided with a first collar 21, similarly, the inner wall surface of the centrifugal impeller 3 adjace...
PUM
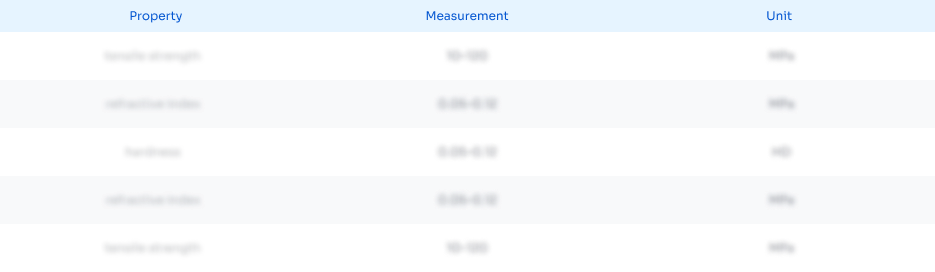
Abstract
Description
Claims
Application Information

- R&D
- Intellectual Property
- Life Sciences
- Materials
- Tech Scout
- Unparalleled Data Quality
- Higher Quality Content
- 60% Fewer Hallucinations
Browse by: Latest US Patents, China's latest patents, Technical Efficacy Thesaurus, Application Domain, Technology Topic, Popular Technical Reports.
© 2025 PatSnap. All rights reserved.Legal|Privacy policy|Modern Slavery Act Transparency Statement|Sitemap|About US| Contact US: help@patsnap.com