Air bag pressurization sealing method for vacuum heat insulation plate
A technology of vacuum heat insulation panels and airbags, applied in the direction of heat insulation protection pipelines, heat exchange equipment, heat preservation, etc., can solve the problems of high cost and failure rate, complex equipment, etc., and achieve simple structure, uniform strength, and heat sealing effect Good results
- Summary
- Abstract
- Description
- Claims
- Application Information
AI Technical Summary
Problems solved by technology
Method used
Image
Examples
Embodiment Construction
[0013] see figure 1 with figure 2 In this embodiment of the present invention, a sealing method for airbag pressurized vacuum insulation panels includes at least one pair of heat-sealing strips arranged in parallel in the frame 1, each of which is composed of an upper heat-sealing strip 3 and a lower heat-sealing strip 3. The sealing strip 4 is composed of an air bag 2 on the upper side of the upper heat sealing strip 3; the sealing edges of the two ends of the vacuum insulation board 10 are placed between the upper heat sealing strip 3 and the lower heat sealing strip 4; the valve 6 is opened to fill the air bag 2 The high-pressure air from the air source (such as an air storage tank) 8, when the air pressure value reaches the set value, that is, after the airbag inflation time is maintained for 8 seconds, the valve 6 is closed to complete a sealing process. Utilize the expansion of the air bag 2 to push the upper and lower heat-sealing strips 3 and 4 to squeeze relatively ...
PUM
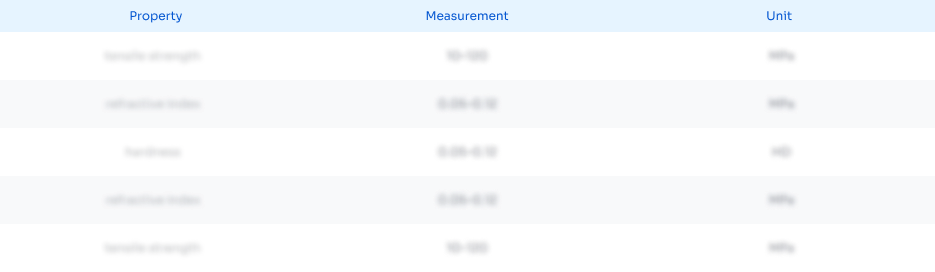
Abstract
Description
Claims
Application Information

- Generate Ideas
- Intellectual Property
- Life Sciences
- Materials
- Tech Scout
- Unparalleled Data Quality
- Higher Quality Content
- 60% Fewer Hallucinations
Browse by: Latest US Patents, China's latest patents, Technical Efficacy Thesaurus, Application Domain, Technology Topic, Popular Technical Reports.
© 2025 PatSnap. All rights reserved.Legal|Privacy policy|Modern Slavery Act Transparency Statement|Sitemap|About US| Contact US: help@patsnap.com