Finite Element Calculation Method of Simplified Model of Large Diameter Tube for Heat Exchange Tube
A calculation method and technology for simplifying models, applied in the direction of calculation, special data processing applications, instruments, etc., can solve the problems of huge calculation amount, high calculation cost, and large limitation, achieve model simplification, improve design efficiency, and reduce calculation cost Effect
- Summary
- Abstract
- Description
- Claims
- Application Information
AI Technical Summary
Problems solved by technology
Method used
Image
Examples
Embodiment 1
[0029] A heat exchanger tube sheet, which consists of: a tube sheet main body, the heat exchange tubes on the tube sheet main body are calculated using the finite element calculation method of a simplified model of a large-diameter tube to obtain the structural size, and the boiler heat exchange tubes are first selected as 2 Based on the calculation of the level equivalent model, the number of equivalent heat exchange tubes of the boiler heat exchange tubes is 9; the cross-sectional area of each heat exchange tube of the equivalent boiler heat exchange tube Am=A / 9=126375 mm 2 ; Select the inner diameter of the heat exchange tube of the equivalent boiler heat exchange tube as 200mm, and the outer diameter of the heat exchange tube of the equivalent boiler heat exchange tube is 448mm; use the symmetry of the model to establish a 1 / 4 overall model, and mesh the model After the equivalent boiler heat exchange tube is 9 heat exchange tubes, the ratio of the outer surface area is 4...
Embodiment 2
[0031] In the calculation process of the heat exchanger tube sheet strength, the heat exchange tube adopts the finite element calculation method of the simplified model of the large-diameter tube. The calculation method is divided into six steps. The first step is to establish a simplified finite element calculation model, and the heat exchange tube Through multi-series equivalent; the second step is to determine the number of heat exchange tubes in the a-level model according to the finite element calculation model; the third step is to determine the number of heat exchange tubes in the a-level layout according to the number of a-level model heat exchange tubes , the fourth step is to determine that the sum of the cross-sectional areas of the heat exchange tubes after the equivalent is equal to the sum of the cross-sectional areas of the heat exchange tubes before the equivalent; the fifth step is to arrange the heat exchange tubes at all levels alternately; The equivalent of ...
Embodiment 3
[0033] In the calculation process of the heat exchanger tube sheet strength, the heat exchange tube adopts the large-diameter tube simplified model finite element calculation method, and the number of heat exchange tubes in the a-level model includes the number of 1-n level model heat exchange tubes , the number of heat exchange tubes in the first-level model is 1, the number of heat exchange tubes in the second-level model is 9, the number of heat exchange tubes in the third-level model is 25, and the n The number of heat exchange tubes in the stage model is (2n-1) 2 .
PUM
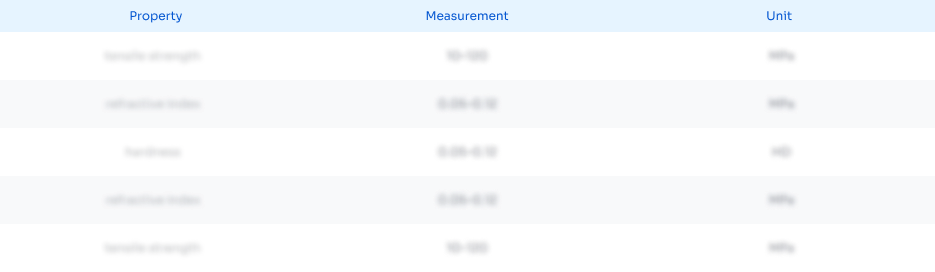
Abstract
Description
Claims
Application Information

- R&D
- Intellectual Property
- Life Sciences
- Materials
- Tech Scout
- Unparalleled Data Quality
- Higher Quality Content
- 60% Fewer Hallucinations
Browse by: Latest US Patents, China's latest patents, Technical Efficacy Thesaurus, Application Domain, Technology Topic, Popular Technical Reports.
© 2025 PatSnap. All rights reserved.Legal|Privacy policy|Modern Slavery Act Transparency Statement|Sitemap|About US| Contact US: help@patsnap.com