Powered artificial knee with agonist-antagonist actuation
An artificial and dynamic technology, applied in the field of dynamic artificial knee joints, can solve the problems of not being able to replicate the active working phase of human knee joints, and not being able to generate active mechanical energy
- Summary
- Abstract
- Description
- Claims
- Application Information
AI Technical Summary
Problems solved by technology
Method used
Image
Examples
Embodiment Construction
[0035] According to the present invention, a variable damping knee prosthesis has two elastic actuators in series arranged in parallel in a main contractor-antagonist arrangement (arrangement). The prosthetic knee model consists of a variable damper and two elastic clutch units in series across the knee joint. The variable damping control design produces a mechanical structure similar to the human knee when walking on steady-state flat ground. Due to the variable damping properties of the prosthesis, its electrical power requirement during walking is moderate, which allows for an energy-saving dynamic knee. In one application, the variable impedance knee prosthesis according to the invention is advantageously used as part of an untethered (non-restrained) biological robotic leg.
[0036] As used herein, the following terms specifically include, but are not limited to:
[0037] As defined below, "actuator" refers to a type of motor.
[0038] "Primary constrictor" refers to a...
PUM
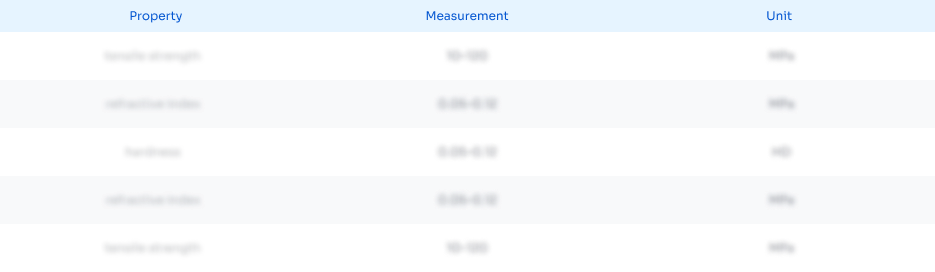
Abstract
Description
Claims
Application Information

- R&D Engineer
- R&D Manager
- IP Professional
- Industry Leading Data Capabilities
- Powerful AI technology
- Patent DNA Extraction
Browse by: Latest US Patents, China's latest patents, Technical Efficacy Thesaurus, Application Domain, Technology Topic, Popular Technical Reports.
© 2024 PatSnap. All rights reserved.Legal|Privacy policy|Modern Slavery Act Transparency Statement|Sitemap|About US| Contact US: help@patsnap.com