Method for producing isopropylbenzene by using benzene and propylene
A technology of cumene and polycumene, applied in the field of cumene production, can solve the problem of high n-propylbenzene content, achieve the effect of reducing content and improving product quality
- Summary
- Abstract
- Description
- Claims
- Application Information
AI Technical Summary
Problems solved by technology
Method used
Image
Examples
Embodiment 1
[0027] according to figure 1 The technological process, the catalyst bed of the alkylation reactor is divided into four sections, loaded with 200 grams of shaped catalyst containing MCM-22 zeolite, each section is equipped with 50 grams, and propylene is fed in four sections. The reaction conditions of the alkylation reactor are: reaction temperature 135°C, reaction pressure 2.3MPa, benzene feed rate into the alkylation reactor 780 g / h, propylene feed rate 200 g / h, each section 50 g / h Hour.
[0028]The first transalkylation reactor was charged with 100 grams of shaped catalyst containing Beta zeolite and the second transalkylation reactor was charged with 50 grams of shaped catalyst containing MCM-22 zeolite. The reaction conditions of the first transalkylation reactor are: 150 DEG C of reaction temperature, 1.2MPa of reaction pressure, 100 grams / hour of polycumene feeding amount (streaming 13), 150 grams / hour of benzene feeding amount (streaming 10) . Wherein, the diisopro...
Embodiment 2
[0035] Same as [Example 1], except that the catalyst bed of the alkylation reactor is divided into four sections, and 170 grams of shaped catalysts containing MCM-22 zeolite are loaded, and 35, 40, 45, and 50 grams of propylene are loaded in the four sections successively. Four stage feeding. The reaction conditions of the alkylation reactor are: reaction temperature 140°C, reaction pressure 2.5MPa, benzene feed rate into the alkylation reactor 600 g / h, propylene feed rate 170 g / h, propylene feed into the four stages in sequence The amount is 35, 40, 45, 50 g / h.
[0036] The first transalkylation reactor was loaded with 50 grams of shaped catalyst containing Beta zeolite, and the second transalkylation reactor was loaded with 50 grams of shaped catalyst containing MCM-22 zeolite. The reaction conditions of the first transalkylation reactor are: reaction temperature 150° C., reaction pressure 1.2 MPa, polycumene feed rate 70 g / hour, benzene feed rate 140 g / hour. Wherein, the ...
Embodiment 3
[0043] Same as [Example 2], except that the reaction conditions of the alkylation reactor are: reaction temperature 135° C., reaction pressure 2.5 MPa, benzene feed into the alkylation reactor 600 g / h, propylene feed 120 g / h Hour.
[0044] The first transalkylation reactor was charged with 50 grams of shaped catalyst containing Beta zeolite and the second transalkylation reactor was charged with 50 grams of shaped catalyst containing MCM-56 zeolite. The reaction conditions of the first transalkylation reactor are: reaction temperature 148° C., reaction pressure 1.1 MPa, polycumene feed rate 70 g / hour, benzene feed rate 140 g / hour. Wherein, the diisopropylbenzene content in the stream 13 is 98%. The reaction conditions of the second transalkylation reactor are: reaction temperature 170° C., reaction pressure 1.5 MPa, polycumene feed rate 100 g / hour, benzene feed rate 100 g / hour. Wherein, the content of triisopropylbenzene in stream 14 is 5%.
[0045] Reaction result: the yie...
PUM
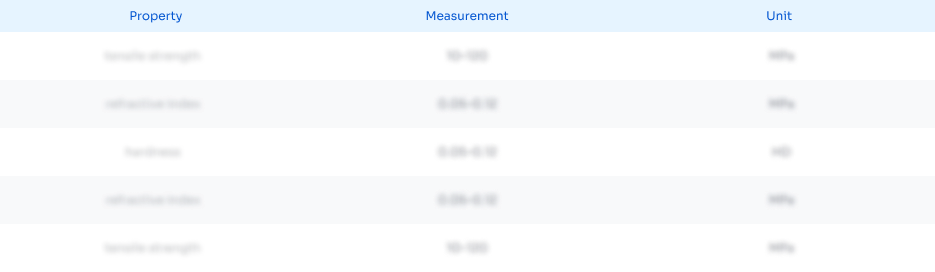
Abstract
Description
Claims
Application Information

- Generate Ideas
- Intellectual Property
- Life Sciences
- Materials
- Tech Scout
- Unparalleled Data Quality
- Higher Quality Content
- 60% Fewer Hallucinations
Browse by: Latest US Patents, China's latest patents, Technical Efficacy Thesaurus, Application Domain, Technology Topic, Popular Technical Reports.
© 2025 PatSnap. All rights reserved.Legal|Privacy policy|Modern Slavery Act Transparency Statement|Sitemap|About US| Contact US: help@patsnap.com