Method for producing isopropylbenzene
A production method and technology of cumene, applied in the direction of chemical instruments and methods, hydrocarbons, hydrocarbons, etc., can solve the problem of high n-propylbenzene content, achieve the effect of reducing content, good technical effect, and improving product quality
- Summary
- Abstract
- Description
- Claims
- Application Information
AI Technical Summary
Problems solved by technology
Method used
Image
Examples
Embodiment 1
[0023] according to figure 1 The technical process, the first transalkylation reactor is loaded with the shaped catalyst of 20 grams of Beta zeolite, and the second transalkylation reactor is loaded with the shaped catalyst of 50 grams of MCM-22 zeolite. The reaction condition of the first transalkylation reactor is: 150 ℃ of reaction temperature, reaction pressure 1.2MPa, the first benzene flow rate (stream 7) 40 grams / hour, many substituted cumene (stream 13) feed rate 20 grams / hour Hours, the content of dicumylbenzene in stream 13 was 98%. The second transalkylation reactor reaction condition is: 180 ℃ of reaction temperature, reaction pressure 1.5MPa, the second benzene flow (stream 8) 80 grams / hour, many substituted cumene (stream 12) flow 80 grams / hour, Triisopropylbenzene content in stream 12 is 10%. Continuous reaction for 5 days.
[0024] The operating conditions of the multi-substituted cumene tower are: tower top temperature 132°C, tower bottom temperature 215°C,...
Embodiment 2
[0027] according to figure 1 The process flow, the first transalkylation reactor is loaded with the shaped catalyst of 30 grams of Beta zeolite, and the second transalkylation reactor is loaded with the shaped catalyst of 40 grams of MCM-22 zeolite. The reaction conditions of the first transalkylation reactor are: 143°C of reaction temperature, 1.2MPa of reaction pressure, 60 g / hour of the first stream of benzene flow (stream 7), and 20 g / h of multi-substituted cumene (stream 13) feed rate Hours, the content of dicumyl in stream 13 was 99%. The second transalkylation reactor reaction condition is: 175 ℃ of reaction temperature, reaction pressure 1.5MPa, the second benzene flow (stream 8) 60 grams / hour, many substituted cumene (stream 12) flow 40 grams / hour, The content of triisopropylbenzene in stream 12 is 8%. Continuous reaction for 5 days.
[0028] The operating conditions of the multi-substituted cumene tower are: tower top temperature 128°C, tower bottom temperature 20...
Embodiment 3
[0031] according to figure 1The technical process, the first transalkylation reactor is loaded with the shaped catalyst of 50 grams of Beta zeolite, and the second alkylation reactor is loaded with the shaped catalyst of 40 grams of SHY-1 zeolite. The reaction conditions of the first transalkylation reactor are: 150 DEG C of reaction temperature, 1.2MPa of reaction pressure, 100 grams / hour of the first stream of benzene flow (stream 7), 60 grams / hour of multi-substituted cumene (stream 13) feeding rate Hours, the content of dicumylbenzene in stream 13 was 98%. The second transalkylation reactor reaction condition is: 180 ℃ of reaction temperature, reaction pressure 1.5MPa, the second benzene flow (stream 8) 80 grams / hour, many substituted cumene (stream 12) flow 80 grams / hour, The content of triisopropylbenzene in stream 12 is 5%. Continuous reaction for 5 days.
[0032] The operating conditions of the multi-substituted cumene tower are: tower top temperature 132°C, tower b...
PUM
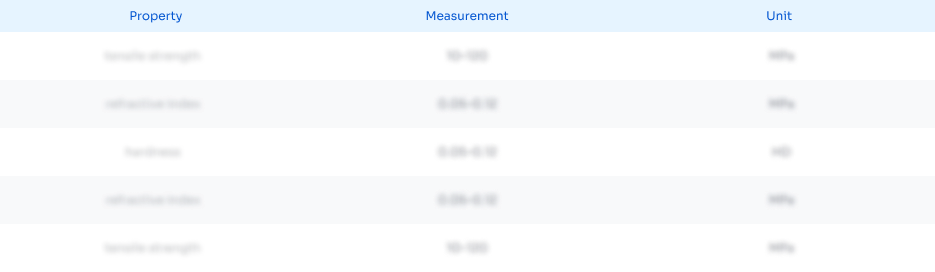
Abstract
Description
Claims
Application Information

- R&D
- Intellectual Property
- Life Sciences
- Materials
- Tech Scout
- Unparalleled Data Quality
- Higher Quality Content
- 60% Fewer Hallucinations
Browse by: Latest US Patents, China's latest patents, Technical Efficacy Thesaurus, Application Domain, Technology Topic, Popular Technical Reports.
© 2025 PatSnap. All rights reserved.Legal|Privacy policy|Modern Slavery Act Transparency Statement|Sitemap|About US| Contact US: help@patsnap.com