Automatic tension control system and method thereof
A control system and tensioning technology, applied in the control/regulation system, non-electric variable control, mechanical pressure/force control, etc., can solve the problems of difficult quality monitoring, low tensioning accuracy, unsafe construction, etc., to avoid Electromagnetic interference, improve the tensioning accuracy, and avoid the effect of large measurement errors
- Summary
- Abstract
- Description
- Claims
- Application Information
AI Technical Summary
Problems solved by technology
Method used
Image
Examples
Embodiment 1
[0056] figure 1 Disclosed in is an automatic tensioning control system, including an electric oil pump 1, a hydraulic jack 2 controlled by the electric oil pump 1, and the automatic tensioning control system also includes an automatic tensioning control system controller 3, a data relay Controller 4 and computer 5. The hydraulic jack 2 is equipped with a rod-type displacement sensor 201 that can move with the piston rod, and the rod-type displacement sensor 201 is fixedly installed on the outer circle of the hydraulic jack cylinder (see Figure 3 ~ Figure 4 ), the piston extension 205 of the hydraulic jack is fixedly equipped with a U-shaped connecting plate 204 with a U-shaped groove on the outer circle, and a guide plate 203 that can slide along the U-shaped groove is installed in the U-shaped groove of the U-shaped connecting plate 204 , the guide plate 203 and the pull rod end of the pull rod displacement sensor 201 are connected together by a nut; a piston anti-rotation ...
Embodiment 2
[0060] Image 6 Disclosed in is an automatic tensioning control system for synchronous tensioning control of two hydraulic jacks, which includes two sets of automatic tensioning control system A6 and automatic tensioning control system B7, wherein the automatic tensioning control System A6 is the automatic tension control system described in Embodiment 1, and its detailed structure will not be repeated; the structure of automatic tension control system B7 is basically the same as the automatic tension control system described in Embodiment 1, the difference is that : The automatic tensioning control system B7 does not include the data relay controller 4 and the computer 5, the output end of the drive module 307 of the automatic tensioning control system controller of the automatic tensioning control system B is connected with the automatic tensioning control through the signal transmission cable The input terminal of the data relay controller 4 of system A is connected, so tha...
Embodiment 3
[0063] An automatic tension control method, which is a method of tension control using the automatic tension control system described in Embodiment 1, which includes the following steps (see Figure 7 ):
[0064] Sep1, start the computer 5 and the automatic tension control system controller 3, the automatic tension control system controller 3 sends signals to the four stepper motors 101, and the four stepper motors 101 are all reversed (that is, reversed). Automatically stop when unable to rotate;
[0065] Sep2, the automatic tensioning control system controller 3 sends a closing signal to the relay K104, the relay K104 is connected, the relay K104 controls the main relay 103 of the main motor 102, at this time the main motor 102 is energized, and the electric oil pump 1 starts to work;
[0066] Sep 3. The pressure sensor 202 located on the oil inlet and oil return nozzle of the hydraulic jack is powered on and started to work, and set to zero;
[0067] Sep 4. The controller...
PUM
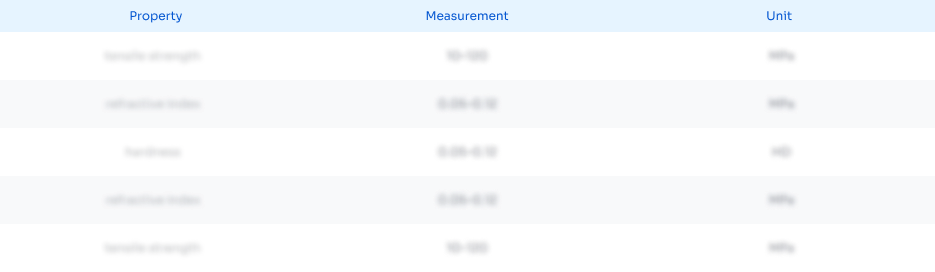
Abstract
Description
Claims
Application Information

- Generate Ideas
- Intellectual Property
- Life Sciences
- Materials
- Tech Scout
- Unparalleled Data Quality
- Higher Quality Content
- 60% Fewer Hallucinations
Browse by: Latest US Patents, China's latest patents, Technical Efficacy Thesaurus, Application Domain, Technology Topic, Popular Technical Reports.
© 2025 PatSnap. All rights reserved.Legal|Privacy policy|Modern Slavery Act Transparency Statement|Sitemap|About US| Contact US: help@patsnap.com