Shock tunnel
A technology of shock wave wind tunnel and inner channel, which is applied in the direction of measuring devices, instruments, aerodynamic tests, etc., can solve problems such as difficulty in meeting the operating conditions of the suture contact surface, increased wind tunnel test time, and reduced wind tunnel driving capacity. Achieve the effects of avoiding boundary layer separation, large separation and unstable vortex, improving flow quality, and improving uniformity and stability
- Summary
- Abstract
- Description
- Claims
- Application Information
AI Technical Summary
Problems solved by technology
Method used
Image
Examples
Embodiment Construction
[0014] Such as figure 1 As shown, the shock tunnel of the present invention includes: a driving section 1 and a driven section 4 , and the inner channel diameter of the driven section 4 is larger than the inner channel diameter of the driving section 1 . A transition section 3 is arranged between the driving section 1 and the driven section 4, and the channel diameter in the section of the transition section 3 gradually increases from the driving section 1 to the driven section 4, and one end of the transition section 3 connected to the driving section 1 The channel diameter in the segment of the segment is the same as that of the driving segment 1, and the channel diameter in the segment at the end of the transition segment 3 connected to the driven segment 4 is the same as that of the driven segment 4. A diaphragm 2 is also arranged between the transition section 3 and the drive section 1 .
[0015] In the embodiment of the present invention, the channel in the transition s...
PUM
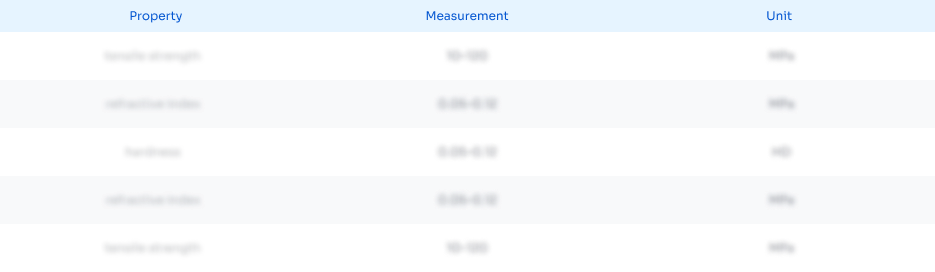
Abstract
Description
Claims
Application Information

- Generate Ideas
- Intellectual Property
- Life Sciences
- Materials
- Tech Scout
- Unparalleled Data Quality
- Higher Quality Content
- 60% Fewer Hallucinations
Browse by: Latest US Patents, China's latest patents, Technical Efficacy Thesaurus, Application Domain, Technology Topic, Popular Technical Reports.
© 2025 PatSnap. All rights reserved.Legal|Privacy policy|Modern Slavery Act Transparency Statement|Sitemap|About US| Contact US: help@patsnap.com