Adaptive control method for increasing thickness precision of finish-rolled band steel by utilizing roll gap
A control method and roll gap technology, applied in the direction of rolling force/roll gap control, etc., can solve the problems of large jumps in rolling plan specifications, poor strip thickness accuracy, and large strip temperature fluctuations.
- Summary
- Abstract
- Description
- Claims
- Application Information
AI Technical Summary
Problems solved by technology
Method used
Image
Examples
Embodiment 1
[0074] A control method for improving the thickness accuracy of finished strip steel by self-adaptation of roll gap, comprising the following steps:
[0075] Step 1. Create a static table of roll gap correction indexed by strip layer. The three parameters of steel type classification, thickness grade and width grade are exactly the same. The initial value of the correction amount is set to 0, and whenever the strip layer is switched, the roll gap correction amount is obtained from the table before rolling, and the roll gap correction amount of the corresponding layer is updated after rolling;
[0076] Step 2: Correct the current value of the roll gap before rolling the k-th coil and the zero-point correction current value of the i-th rack Added together, the learning coefficient of the roll gap model of the k-th coil and the i-stand is obtained, which is used for the pre-calculation of the rolling setting of the k-th coil,
[0077] 1) if figure 2 As shown, the current va...
PUM
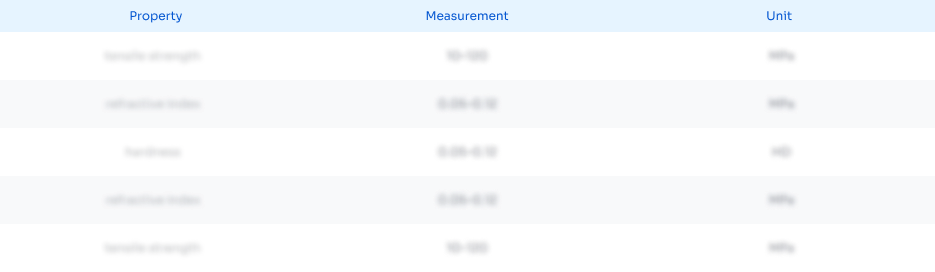
Abstract
Description
Claims
Application Information

- Generate Ideas
- Intellectual Property
- Life Sciences
- Materials
- Tech Scout
- Unparalleled Data Quality
- Higher Quality Content
- 60% Fewer Hallucinations
Browse by: Latest US Patents, China's latest patents, Technical Efficacy Thesaurus, Application Domain, Technology Topic, Popular Technical Reports.
© 2025 PatSnap. All rights reserved.Legal|Privacy policy|Modern Slavery Act Transparency Statement|Sitemap|About US| Contact US: help@patsnap.com