Clamp device for carrying out groove milling on wheel disk of gas turbine
A gas turbine and fixture device technology, applied in positioning devices, clamping, manufacturing tools, etc., can solve problems such as difficult positioning and clamping, and achieve the effects of simple structure, convenient use, and easy manufacturing
- Summary
- Abstract
- Description
- Claims
- Application Information
AI Technical Summary
Problems solved by technology
Method used
Image
Examples
specific Embodiment approach 1
[0007] Specific embodiment one: combination figure 1 with figure 2 To explain this embodiment, a clamp device for milling grooves in a gas turbine wheel disc includes a base 1, a support frame 3, a positioning pin 4, a clamp body 5, a gland 6, a double-ended screw 7, a nut 8, and a The indexing table 16, a plurality of positioning pins 12, a plurality of first positioning keys 13 and a plurality of pressing plates 14, the base 1, the indexing table 16, the clamp body 5 and the pressing cover 6 are arranged from bottom to top, the base 1 and the indexing table 16 is fixed by a plurality of pressing plates 14, the indexing table 16 and the clamping body 5 are positioned by a plurality of first positioning keys 13, the clamping body 5 and the pressing cover 6 are positioned by a plurality of positioning pins 12, and the clamping The concrete 5 and the gland 6 are fixed by a double-headed screw 7 and a nut 8. The supporting frame 3 is arranged between the base 1 and the clamping b...
specific Embodiment approach 2
[0010] Specific implementation manner two: combination figure 1 with figure 2 To illustrate this embodiment, a clamp device for milling grooves in a gas turbine wheel disc of this embodiment further includes a plurality of second positioning keys 17, and the base 1 is provided with a first key groove 1-1 and a second key groove 1-2, A third keyway 16-1 and a fourth keyway 16-2 are opened on the bottom surface of the indexing table 16. The first keyway 1-1 is matched with the third keyway 16-1, and the second keyway 1-2 and the fourth keyway 16 -2 is matched, the first keyway 1-1 and the third keyway 16-1 and the second keyway 1-2 and the fourth keyway 16-2 are positioned and connected by a plurality of second positioning keys 17. This arrangement facilitates the precise positioning of the base 1 and the indexing table 16. The other composition and connection relationship are the same as in the first embodiment.
specific Embodiment approach 3
[0011] Specific implementation mode three: combination figure 1 with figure 2 To describe this embodiment, the lower end of the support frame 3 of this embodiment is fixedly mounted on the base 1. This setting facilitates the precise positioning of the entire fixture. The other composition and connection relationship are the same as in the second embodiment.
PUM
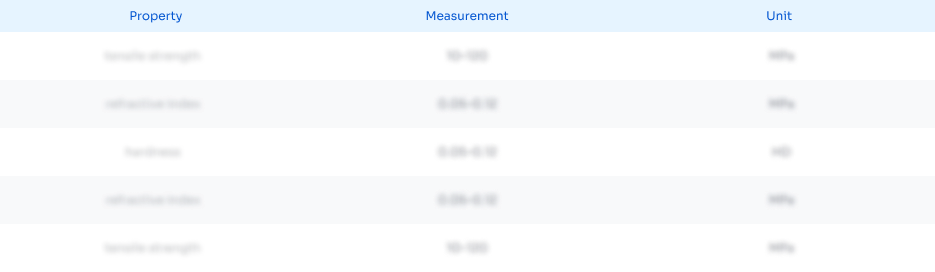
Abstract
Description
Claims
Application Information

- R&D
- Intellectual Property
- Life Sciences
- Materials
- Tech Scout
- Unparalleled Data Quality
- Higher Quality Content
- 60% Fewer Hallucinations
Browse by: Latest US Patents, China's latest patents, Technical Efficacy Thesaurus, Application Domain, Technology Topic, Popular Technical Reports.
© 2025 PatSnap. All rights reserved.Legal|Privacy policy|Modern Slavery Act Transparency Statement|Sitemap|About US| Contact US: help@patsnap.com