Molding die for processing high-tension plate parts
A molding die and high tension technology, applied in the stamping field of automobile structural parts, can solve the problems of insufficient plastic deformation molding, difficult molding of high tension plate parts, warping of flange edges, etc., to achieve simple manufacturing process and low maintenance cost. , the effect of sufficient blank holder force
- Summary
- Abstract
- Description
- Claims
- Application Information
AI Technical Summary
Problems solved by technology
Method used
Image
Examples
Embodiment Construction
[0036] Below in conjunction with accompanying drawing, the present invention will be further described:
[0037] image 3 and Figure 4 It shows a structural schematic diagram of a molding die for processing high-tensile plate parts, including an upper die base 11, a pressing core 13, an upper die fixing plate 14, a lower die base 15, a punch 17, a pressing plate 18 and an upper die block 19. The upper mold fixing plate 14 is arranged between the upper mold base 11 and the upper mold knife block 19 , and the pressing core 13 passes through the upper mold fixing plate 14 . At least one first nitrogen gas spring 12 is arranged between the pressing core 13 and the upper die base 11 , and the pressing core 13 can move vertically relative to the upper die fixing plate 14 under the action of the first nitrogen gas spring 12 . At least two second nitrogen gas springs 16 are arranged between the binder plate 18 and the lower mold base 15, and at least two second nitrogen gas springs...
PUM
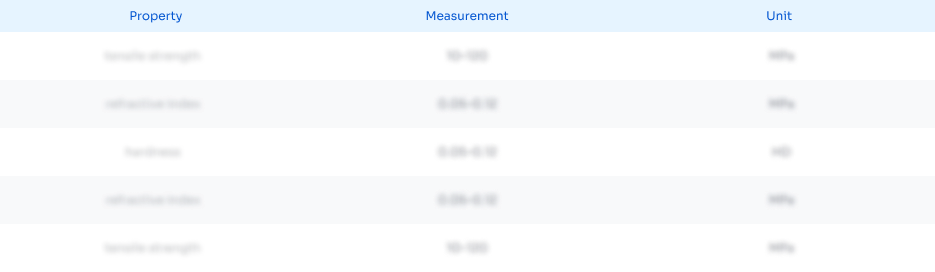
Abstract
Description
Claims
Application Information

- R&D
- Intellectual Property
- Life Sciences
- Materials
- Tech Scout
- Unparalleled Data Quality
- Higher Quality Content
- 60% Fewer Hallucinations
Browse by: Latest US Patents, China's latest patents, Technical Efficacy Thesaurus, Application Domain, Technology Topic, Popular Technical Reports.
© 2025 PatSnap. All rights reserved.Legal|Privacy policy|Modern Slavery Act Transparency Statement|Sitemap|About US| Contact US: help@patsnap.com