Oven-drying working process for coke dry quenching system
A technology of CDQ and CDQ, which is applied in the oven process field of CDQ system, can solve the problems of cracking of refractory materials, inability to timely and accurately judge the drying condition of CDQ, and temperature rise, etc., so as to prolong the service life , The effect of shortening the start-up time of the oven
- Summary
- Abstract
- Description
- Claims
- Application Information
AI Technical Summary
Problems solved by technology
Method used
Image
Examples
Embodiment 1
[0026] Embodiment 1: As shown in the figure, the CDQ system oven start-up process includes the following steps:
[0027] Step 1, warm air drying CDQ furnace,
[0028] Step 2, after step 1 is finished, carry out gas drying CDQ,
[0029] Step 3. After step 2 is completed, put red coke into the CDQ furnace to raise the temperature of the refractory material to 1050°C at a rate of 30°C / h, and complete the oven operation. During this process, nitrogen gas is continuously fed into the CDQ furnace Replace the combustible gas in the furnace, and replace the combustible gas to avoid the explosion hazard caused by the accumulation of combustible gas; put in red coke to heat up the CDQ furnace, and transfer the test data before the official work of the CDQ furnace to ensure the smooth operation of the CDQ furnace Carry out; of course, in specific implementation, the heating rate of the refractory material in this step can also be other values within the range of <30°C / h, and the final...
Embodiment 2
[0039]Embodiment 2: As shown in the figure, the CDQ system oven start-up process includes the following steps:
[0040] Step 1, warm air drying CDQ furnace,
[0041] Step 2, after step 1 is finished, carry out gas drying CDQ,
[0042] Step 3. After step 2 is completed, put red coke into the CDQ furnace to raise the temperature of the refractory material to 1000°C at a rate of 25°C / h to complete the oven operation. During this process, nitrogen gas is continuously fed into the CDQ furnace Replace the combustible gas in the furnace, and replace the combustible gas to avoid the explosion hazard caused by the accumulation of combustible gas; put in red coke to heat up the CDQ furnace, and transfer the test data before the official work of the CDQ furnace to ensure the smooth operation of the CDQ furnace conduct;
[0043] Described step 1 comprises the following operations:
[0044] a. The air is passed into the boiler, and the boiler uses low-pressure steam to heat the air, and...
Embodiment 3
[0052] Embodiment 3: As shown in the figure, the CDQ system oven start-up process includes the following steps:
[0053] Step 1, warm air drying CDQ furnace,
[0054] Step 2, after step 1 is finished, carry out gas drying CDQ,
[0055] Step 3. After step 2 is completed, red coke is loaded into the CDQ furnace to raise the temperature of the refractory material to 950°C at a rate of 20°C / h, and the oven operation is completed. During this process, nitrogen gas is continuously fed into the CDQ furnace Replace the combustible gas in the furnace, and replace the combustible gas to avoid the explosion hazard caused by the accumulation of combustible gas; put in red coke to heat up the CDQ furnace, and transfer the test data before the official work of the CDQ furnace to ensure the smooth operation of the CDQ furnace conduct;
[0056] Described step 1 comprises the following operations:
[0057] a. The air is passed into the boiler, and the boiler uses low-pressure steam to heat ...
PUM
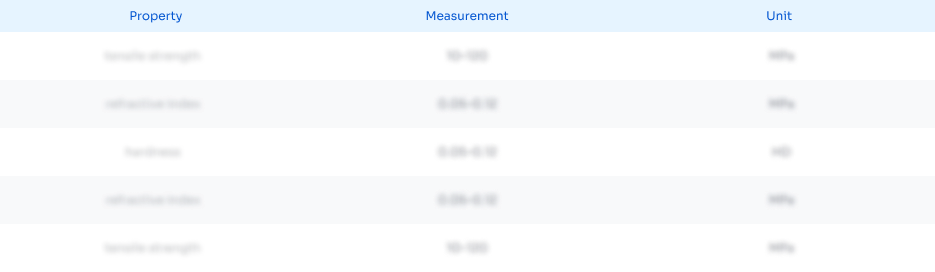
Abstract
Description
Claims
Application Information

- R&D Engineer
- R&D Manager
- IP Professional
- Industry Leading Data Capabilities
- Powerful AI technology
- Patent DNA Extraction
Browse by: Latest US Patents, China's latest patents, Technical Efficacy Thesaurus, Application Domain, Technology Topic, Popular Technical Reports.
© 2024 PatSnap. All rights reserved.Legal|Privacy policy|Modern Slavery Act Transparency Statement|Sitemap|About US| Contact US: help@patsnap.com