A method of casting transformer coils and a special mold
A technology of transformer coils and molds, which is applied in the manufacture of inductors/transformers/magnets, household appliances, and other household appliances, can solve the problems of non-adjustable height, poor versatility, and long processing cycle, so as to reduce production costs and save money. Material and processing costs, the effect of easy processing
- Summary
- Abstract
- Description
- Claims
- Application Information
AI Technical Summary
Problems solved by technology
Method used
Image
Examples
Embodiment Construction
[0018] The present invention will be further described through the embodiments below in conjunction with the accompanying drawings.
[0019] A special mold for casting transformer coils, comprising a cross 1, an upper end plate 2, an upper positioning plate 3, an inner mold 5, an outer mold 6, a lower positioning plate 7, and a lower end plate 8, the lower positioning plate is connected to the lower end plate, and the upper positioning plate The extension part is connected with the upper end plate, the inner mold is placed between the upper positioning plate and the lower positioning plate, the inner mold is connected with the upper end plate and the lower end plate by a screw, the outer mold and the inner mold are arranged in parallel longitudinally, the outer mold and the cross, The screw rods are used to compress the connection between the lower end plates.
[0020] The lower positioning plate and the lower end plate are fixedly connected by bolts; the extension part of the...
PUM
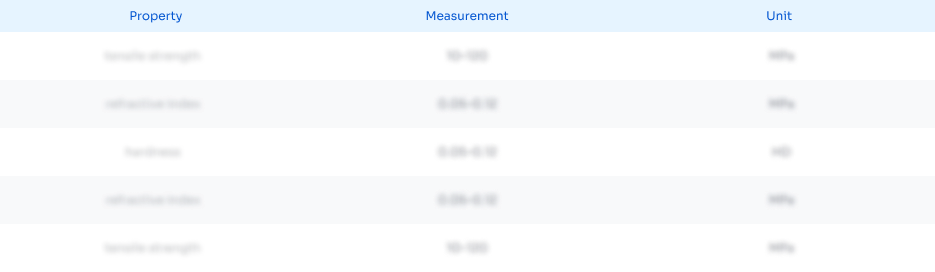
Abstract
Description
Claims
Application Information

- R&D
- Intellectual Property
- Life Sciences
- Materials
- Tech Scout
- Unparalleled Data Quality
- Higher Quality Content
- 60% Fewer Hallucinations
Browse by: Latest US Patents, China's latest patents, Technical Efficacy Thesaurus, Application Domain, Technology Topic, Popular Technical Reports.
© 2025 PatSnap. All rights reserved.Legal|Privacy policy|Modern Slavery Act Transparency Statement|Sitemap|About US| Contact US: help@patsnap.com